Mill Balls Composition

Cast Grinding Steel Balls - 911 Metallurgist
5 天之前 The chemical composition of the high chromium type product should conform to the below table. We can also manufacture the product
More
Chemical composition of selected grinding media (wt.%)
One of the most used tumbling mills is the ball mill. This paper reviews different types of grinding media that have been developed and improved over the years and their properties.
More
Grinding Media - Union Process
Composition. metallic grinding media like carbon steel, forged steel, stainless steel or chrome steel grinding balls are best for some applications, while others require non-metallic media made of alumina, ceramics,
More
(PDF) Grinding Media in Ball Mills-A Review
2023.4.23 Grinding Media in Ball Mills-A Review License CC BY 4.0 Authors: Nyasha Matsanga Willie Nheta Ngonidzashe Chimwani Preprints and early-stage research may not have been peer reviewed yet....
More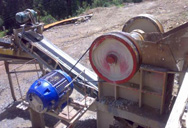
A Review of the Grinding Media in Ball Mills for Mineral
2023.10.27 The performance of grinding media in a ball mill is measured in terms of wear rate, which is a function of the media composition, hardness, phase structure, and
More
Ball size distribution for the maximum production of a
2015.11.1 Introduction. A mix of balls of different diameters enables the effective milling of different particle sizes in a tumbling mill while ensuring the optimisation of the
More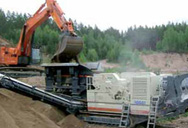
Study on the structure and properties of a novel mini-sized
2002.9.1 To substitute bearing steel mill balls used in magnetic material powder production, a novel mini-sized high Cr mill balls with sizes in the range Ø 6.35–7.14 mm
More
Effect of grinding media on the milling efficiency of a ball mill ...
2022.1.1 The effect of ball load composition, by varying the grinding media size distribution (e.g. alternatively by mixing four groups of 19.5, 38 mm; 19.5, 50 mm; 38, 50
More
Ball Mill - an overview ScienceDirect Topics
Generally, filling the mill by balls must not exceed 30–35% of its volume. Productivity of ball mills depends on drum diameter and the relation of drum diameter and length. Optimum
More
Development of Grinding Media Balls Using Locally
2023.8.1 Microsoft Word - PAPER A11. The Third International Conference on Structure, Processing and Properties of Materials 2010, SPPM 2010. 24- 26 February 2010, Dhaka, Bangladesh, SPPM 2010 A11.
More
Ball Milling in Organic Synthesis: Solutions and Challanges
2011.3.2 It is rather recommend changing reaction time than frequency. Start with 75-100% of the maximal operation frequency of the ball mill. The thermal stress for the reactants could be reduced by using cycled mode: mill for a. specific amount of time – 5-10 min pause – start milling again and repeat the procedure for the required amount of time.
More
邦德球磨功指数试验的影响因素*-Influencing Factors of Bond ...
;Bond ball mill work index is an important tool for the comminution flow-sheet design of mineral processing plant and the efficiency evaluation of comminution circuit performance. The difference of ball composition and mill body structure in different commercial Bond ball mill work index tests has always been ignored.
More
(PDF) Study On The Performance Of High Chromium Cast Iron Balls
2002.8.16 The effect of carbide volume fraction (13-41%) and different matrix microstructures on abrasion-corrosion wear behavior of HCWCI balls tested in a laboratory ball mill for 200 h was studied by ...
More
A Review of the Grinding Media in Ball Mills for Mineral
2023.10.27 The ball mill is a rotating cylindrical vessel with grinding media inside, which is responsible for breaking the ore particles. Grinding media play an important role in the comminution of mineral ores in these mills. This work reviews the application of balls in mineral processing as a function of the materials used to manufacture them and the
More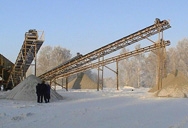
(PDF) Grinding Media in Ball Mills-A Review - ResearchGate
2023.4.23 July 2009 . Farit Urakaev. We will focus on the important aspect of mechanochemical processing by grinding in a ball mill, namely, nanoscale wear of the treated minerals and of the milling tools ...
More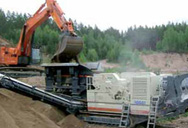
An innovative approach for determining the grinding
2021.1.22 1. Introduction. Grinding operation is used extensively in the industry of beneficiation, metallurgy, chemical engineering, and electric power. Assisted by the impact and abrasion between media (steel ball, steel rod, gravel, ceramic ball) and ore, the grinding operation reduces the particle size in the mill [[1], [2], [3]].To produce the qualified size
More
Grinding Media, Grinding Balls - NETZSCH Grinding
3 天之前 The grinding media, also referred to as grinding balls or grinding beads, serve as the tools in mills with freely moving grinding media, such as agitator ball mills. The movement of these grinding balls within the mill generates various stresses between the balls and the product, including impact, pressure, friction, and shear. Please accept ...
More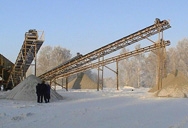
Effect of grinding media on the milling efficiency of a ball mill ...
2022.1.1 The effect of ball load composition, by varying the grinding media size distribution (e.g. alternatively by mixing four groups of 19.5, 38 mm; 19.5, 50 mm; 38, 50 mm and 19.5, 38, 50 mm), on the ...
More
Mixing methods for solid state electrodes: Techniques,
2023.5.15 In ball mill mixers, a jar (sometimes called vessel or bowl) is charged with milling or grinding media (also known as balls or beads) that are moved and mixed with the raw materials and reagents. The ball number, ball to powder ratio (BPR), ball composition and ball diameter must be chosen carefully, as these parameters directly influence the ...
More
Consumption of steel grinding media in mills – A review
2013.8.1 It is generally accepted that highly non-spherical debris from balls which break or spall due to manufacturing defects reduce ball mill grinding performance (Sinnott et al., 2011). More recently, Qian et al. (2013) have investigated the effect of grinding media shapes on the grinding kinetics of cement clinkers in balls mills. The specific ...
More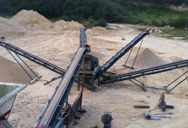
Ball size distribution for the maximum production of a
2015.11.1 Abstract. Ball size distribution is commonly used to optimise and control the quality of the mill product. A simulation model combining milling circuit and ball size distribution was used to determine the best make-up ball charge. The objective function was to find the ball mix that guarantees maximum production of the floatable size range (i.e ...
More
Grinding Media - ME Elecmetal
Chemical composition ranges reported above are for reference only. The specific chemistry of each bar will be determined according to the diameter and hardness level required. ... ME Performa® steel balls for regrinding are designed for ball mill applications and are available in diameters ranging from approximately 7/8” to 1.5” (20-40 mm).
More
Ball Mill - SBM Ultrafine Powder Technology
The composition of the ball mill. The ball mill is composed of main parts such as feeding part, discharging part, rotating part, transmission part (reducer, small transmission gear, motor, electric control). The hollow shaft is made of cast steel, the inner lining can be removed and replaced, the large rotary gear is processed by casting gear ...
More
Alumina Ceramic Ball-Rongsheng High Alumina Refractory
The main composition of alumina ceramic ball is aluminate oxide, which is an excellent refractory material, and has little negative effect on the product being grinded. The balls are manufactured by rolling or isostatic, so it has a high density. And due to the high density, the product can largely promote efficiency of grinding and cut down ...
More
Heat treatment process for high chromium grinding ball
2023.12.1 Ball mill is widely used in building materials, mineral processing, cement, thermal power generation and fertilizer production of the main grinding equipment, grinding ball is the largest consumption of wear-resistant parts. ... The research on high chromium cast iron ball mainly focuses on chemical composition selection, heat treatment process ...
More
Producing Metal Powder from Machining Chips Using Ball
2023.6.27 The balls (Ø 20 mm) reduce the machining chips to a coarse powder. Then balls (Ø 6 mm) formed spherical morphology in the powders with particle sizes ranging from 38 μm to 150 μm (60 h). The ball-milled powder produced from machining chips has a 56% greater hardness than the gas-atomized powder.
More
High-Energy Ball Milling Parameters in Production of
2017.8.24 The minimum achievable grain size and extent of alloying depend on a number of parameters i.e., type of high-energy ball mill, milling container, ball-to-powder weight ratio, milling speed, grinding medium, extent of filling of the vial, milling atmosphere, process controlling agents, milling temperature, type of material being milled etc.
More
Minerals Free Full-Text Study on the Grinding Law of Ball
2022.2.21 Each grinding test exhausted a small bag of 500 g of the test sample. The other grinding conditions, such as the grinding solid concentration, ball filling fraction of the mill volume, ball size, and composition in the case of multi-sized grinding, were set at fixed or varied values, depending on the purposes of the tests.
More
Choose the Best Grinding Steel Balls for Your Ball Mill Fote
2024.1.17 Each grinding balls are round balls with precise dimensions. The sizes of Fote grinding steel balls can be designed according to customer requirements. Generally, the ball diameter is between 20mm and 125mm. You can also design 10mm, 11mm or other diameters of steel balls. Small steel balls: 40mm or 60mm.
More
33 Things You Didn't Know About Ball Mill - ZENITH Crusher
2021.8.24 Answer: to improve the technical efficiency of the mill, the following aspects can be considered: ①. Closed circuit grinding process is adopted. ②. In terms of equipment selection, the rod mill with peripheral discharge should be used for coarse grinding, and the grid ball mill should be used for fine grinding. 30.
More
Resminer High Chrome Grinding Media Balls - Manufacturer
A High Chrome Grinding Media ball is a type of grinding media found in ball mills made from special steel alloy, and it is commonly used for crushing hard materials such as rocks, ores, metals, and so on. It is also called ‘high chromium’ or ‘chrome’ grinding media. Hi-chrome grinding media balls are usually sold in various shapes and ...
More
In ball milling why do we use zirconia balls and vials for the
While you are correct in all you write, we need to note than 99% of the energy in a ball mill is converted to heat, noise, and (some) light. Only around 1% of the energy is actually involved in ...
More
Milling Media and Grinding Balls. Applications and Selection
2018.6.1 Milling media and grinding balls are used for milling or grinding processes to crush, grind and mill various materials. There is a variety of milling media materials such as: Steel (chrome steel, and stainless steel, 304SS and 316SS) and Ceramics (agate, alumina, yttria stabilized zirconia, and tungsten carbide) ... Composition – The ...
More
Planetary Mono Mill PULVERISETTE 6 classic line / 说明
AT A GLANCE. Special grinding force due to a rotational speed up to 650 U/min. Loss-free grinding even below 1 μm. 1 Working station with easily adjustable imbalance compensation. Safe tensioning of the bowls with the Safe-Lock-System. Useful capacity up to 225 ml.
More
Improving the Quality of Steel Grinding Balls - Springer
2017.8.29 HRC 65 are outlined, in terms of the chemical composition of the steel, the equipment required, and the pro- ... Keywords: grinding balls, ball mills, ball production, ball quality, ball-rolling systems DOI: 10.3103/S0967091217020115 In ferrous and nonferrous metallurgy, the cement industry, the power industry, the chemical industry,
More
Ball size distribution for the maximum production of a
2015.11.1 Fig. 5 shows the effects of varying make-up ball composition on the amount of M2 produced for different flow rates in cubic metres per hour. The mill under study has the maximum ball diameter of 40 mm [11]. In this research, the size combinations used were 50 and 40 mm, 40 and 30 mm, 30 and 20 mm and lastly 20 and 15 mm.
More
High Alumina grinding balls China manufacturers
High Alumina grinding balls are grinding media used in ball mill. Alumina ceramic grinding balls can improve the effectively of the grinding. Skip to content +86-17895376160 . ... HIGH Alumina ceramic grinding ball Chemical Composition Technical Parameter. Item. AK-75. AK-92. AK-95. Al2O3 (%) ≧75. ≧92. ≧95. BulK DENSITY (g/cm3) ≧3.20 ...
More
Optimum choice of the make-up ball sizes for maximum
2013.9.1 The optimum composition of the make-up ball sizes in ball mills is presented. • The effect of various factors was investigated via a grinding circuit simulation. • Binary mixtures of two ball sizes always perform better than other mixtures. • An equation is proposed for calculating the optimum composition of the make-up balls.
More
Grinding Balls Rods - 911 Metallurgist
2016.10.20 Grinding Balls. Steel balls ranging from ¾ to 5 in. in diameter are used. Rods range from 1½ to 4 in. in diameter and should be 3 to 4 in. shorter than the inside mill length. Tube mills are usually fed balls smaller than 2 in., whereas 4- or 5-in. balls are more commonly used for ball-mill grinding.
More