flow of washing and crushing iron ore

Comminution and classification technologies of iron ore
2022.1.1 Iron ore crushing and screening. Iron ore is one of the main raw materials to make steel. About 98% of the mined iron ore is used to make steel either by the blast furnace—basic oxygen furnace (BF-BOF) route or through the electrical arc furnace
More
The six main steps of iron ore processing - Multotec
1. Screening We recommend that you begin by screening the iron ore to separate fine particles below the crusher’s CSS before the crushing stage. A static screen is used to
More
Iron ore washing process and equipment LZZG
1 天前 The crushing process of iron ore washing plant generally uses feeders, first crushing, second crushing, screening, and fine crushing. In the production of chromite
More
Iron Ore Processing, General SpringerLink
2022.10.20 Making iron and steel from iron ore requires a long process of mining, crushing, separating, concentrating, mixing, agglomeration (sintering and pelletizing),
More
Development of process for beneficiation of low-grade
2018.12.19 and silica in the iron ore. In preliminary beneficiation studies, the simple techniques of crushing, scrubbing and washing of iron ores met with limited success in
More
Washing SpringerLink
2023.7.22 Washing is the process in which hydraulic or mechanical power is used to wash the ore that is cemented by clay or contains high content of slime, so as to change
More
Crushing characteristics and performance evaluation of iron ore
2023.12.1 In this study, the crushing process of spherical iron ore particles, constructed by an Apollonian sphere packing (ASP) method, was numerically reproduced
More
Iron ore beneficiation: an overview - ScienceDirect
2023.1.1 Dry processing of iron ore: In dry processing of iron ore, ROM is generally crushed below 40 mm through three-stage crushing and thus segregated by screening
More
Research into the crushing and grinding processes of
1 Introduction The effectiveness of simultaneous effect of mechanical load and electric field of ultra-high frequency (UHF) in the process of iron ore crushing is substantiated in
More
Extraction of Iron, Iron Mining, Iron Ore Processing - Xinhai
Extraction of Iron, Iron Mining, Iron Ore Processing. As one of the earliest, most widely used metals in the world, iron ore is an important raw material for iron and steel production. At
More
Minerals Free Full-Text Pre-Processing to Increase the
2022.6.6 A total of 120 t of Cristalino ore was prepared and sent to CIMM, where it was crushed and screened prior to grinding tests. The processing equipment included a 1.83 m (8′) diameter by 0.61 m (2′) length AG/SAG mill equipped with a 20 kW motor, a cone crusher, a 0.91 m (3′) diameter by 1.22 m (4′) length ball mill equipped with a 15 kW ...
More
Crushing and Grinding Wet Sticky Ore - 911
2016.5.9 A washing section is a “must” in all operations handling wet, sticky ore. This facilitates ore handling, crushing, and also affords a means for separation of primary slimes and increasing grinding capacity. These
More
Development of process for beneficiation of low-grade
2018.12.19 Low-grade iron ore received from the West Singhbhum area of Jharkhand state in India was used to develop a beneficiation flow sheet to remove alumina (Al 2 O 3 ) and silica (SiO 2) from the ore to get iron (Fe)-rich product for steel plants. Mineral characterization showed that the main mineral constituents present in the head sample
More
5 Easy but Efficient Steps to Realize Manganese Ore Processing
2023.4.10 The complete processing flow of manganese ore mainly includes five steps: crushing, washing, grinding, dressing, and drying. Next, I will introduce the detailed manganese ore processing production line to you. 1. Manganese ore crushing process and equipment. Manganese ore crushing is the first step in the process, which involves
More
Developments in iron ore comminution and classification
2015.1.1 The largest iron ore company in world, Vale, is developing S11D project, located in the Amazon region of Northern Brazil (Carajás), which is expected to produce 90 million Mtpa of iron ore (Carter, 2011). In designing the innovative, modular ore crushing and screening plant for SD11, Vale was faced with the challenge of coping with the region ...
More
Physical Beneficiation - an overview ScienceDirect Topics
The first step of physical beneficiation is crushing and grinding the iron ore to its liberation size, the maximum size where individual particles of gangue are separated from the iron minerals. A flow sheet of a typical iron ore crushing and grinding circuit is shown in Figure 1.2.2 (based on Ref. [4]).This type of flow sheet is usually followed when the crude ore
More
INTEGRATION OF IRON ORE DEPOSIT EVALUATION
2011.10.14 through primary and secondary crushing followed by screening and oversize crushing and re-screening, washing and sizing, scrubbing, classification in classifier and hydrocyclone, with a overall weight recovery of ... Fig. 2: Process flow of Joda East iron ore processing plants. R. MUKHERJEE, S. VERMA, B.D. MOHANTY, S MOHAN RAO
More
Crushing Plant Design and Layout Considerations - JXSC Mine
For example, the feeding of the autogenous mill is 300 to 500 mm, the particle size of the iron-rich ore smelting in the blast furnace is divided into two stages of 25 ~ 30 and 25 ~ 30 mm. The reasonable ore size of the rod mill is 20 ~ 40, the ball mill has a reasonable ore size of 10 to 25 mm. ... 2.3 Crushing flow with the washing process ...
More
Energy and Environmental Profile of the U.S. Mining
2013.11.8 Table 4-3 shows the estimated energy requirements for a surface iron mine in the U.S. The iron mine operates over a 22-year lifetime with a 110 million-ton output at the end of its life. The mine runs 364 days per year with two 8.00 hour shifts per day, which gives it a daily production rate of 13,699 tons per day.
More
Crushing Circuit - an overview ScienceDirect Topics
The first step of physical beneficiation is crushing and grinding the iron ore to its liberation size, the maximum size where individual particles of gangue are separated from the iron minerals. A flow sheet of a typical iron ore crushing and grinding circuit is shown in Figure 1.2.2 (based on Ref. [4]).This type of flow sheet is usually followed when the crude ore
More
Major Mines Projects Sishen Mine
Sishen Mine is a conventional open pit mining operation applying a pushback deployment strategy. The distinctive mining areas are North Mine (G80 and G50), Middle Mine, Dagbreek, Vliegveld, Far South and Lyleveld. Material is drilled, blasted, loaded by electric and diesel (rope and hydraulic) shovels and hauled by trucks to either the primary ...
More
(PDF) REMOVING IMPURITIES FROM IRON ORES: METHODS
2016.9.1 Overall, the acceptable level of phosphorus, sulphur and silica in the iron concentrate should be less than 0.04%, 0.15 % and 1.5 % respectively. Scarcity of high grade iron ores necessitates ...
More
Iron Mining Process Equipment Flow Cases - JXSC
2023.12.31 150TPH Iron Ore Processing Plant in Malaysia. Material: hard rock type iron ore Capacity: 150TPH Country: Malaysia Feeding size: 0-400mm Raw mineral description: 1. Weak magnetic iron 2. Contains slime 3. Need crushing – washing – magnetic separation flow. Customers requirements: 1. The particle size of finished
More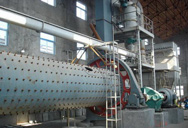
Development of ore sorting and its impact on mineral processing ...
2014.10.15 The energy costs required to refine metal values contained in ore to concentrates constitute the majority of the cost to produce metals. On average across the mining industry, 44% of the total electricity consumption is dedicated to crushing and milling activities (Fig. 1).Size reduction operations, nearly 150 × 10 9 kW h, are the largest
More
Physical separation of iron ore: magnetic separation
2022.1.1 If the gangue mineral in an iron ore is predominantly quartz, reverse flotation is often used in the cleaning stage to improve the concentrate Fe grade. Fig. 9.13 presents a typical flow sheet for processing an oxidized iron ore containing about 30% Fe using a combination of SLon magnetite separators and reverse flotation. The ore is mainly ...
More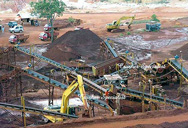
Mining and Beneficiation of Phosphate Ore IntechOpen
2016.4.13 The first commercial production of phosphate rock began in England in 1847. A wide variety of techniques and equipment is used to mine and process phosphate rocks in order to beneficiate low-grade ores and remove impurities. The eighth chapter of this book deals with mining and beneficiation of phosphate ore. The principle and
More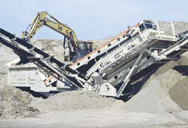
Iron Ore: From Mining to Processing to Dust Control
Iron ore is a rock or mineral from which metallic iron can be extracted economically. It constitutes 5% of the earth’s crust. Viable forms of ore contain between 25% and 60% iron. Ore greater than 60% iron is known as natural ore or direct shipping ore, meaning it can be fed directly into iron-making blast furnaces.
More
Collections: Iron, How Did They Make It? Part I, Mining
2020.9.18 One distinction here is between bog iron and iron in ore deposits. Bog iron is formed when ground-water picks up iron from iron-ore deposits, where that iron is then oxidized under acidic conditions to form chunks of iron minerals (goethite, magnetite, hematite, etc.), typically in smallish chunks.
More
Physical Bauxite Processing: Crushing and Grinding of Bauxite
2022.1.23 3.1 Introduction to Crushing and Grinding of Bauxite. The most common initial process step to feed an alumina refinery with bauxite is the crushing or sizing of the raw bauxite material that is extracted from the mine. The feed material is crushed or sized so that it is conveyable, as well as correctly dimensioned, for the next step in the process.
More
The Aerodynamics of an Iron Ore Pelletizing Rotary Kiln
2022.5.5 This paper summarizes more than a decade of systematic studies of the flow field in an iron ore pelletizing rotary kiln using computational fluid dynamics (CFD) on simplified models of a real kiln. Physical, laser-based experiments have been performed to validate part of the numerical results. The objective is a better understanding of the kiln
More
(PDF) Beneficiation and flowsheet development of
2020.12.1 In the present study a detailed characterization followed by beneficiation of low grade iron ore was studied. The Run of Mine (R.O.M) sample assayed 21.91 % Fe, which is very low grade in nature.
More
Iron Ore Processing - JXSC Mineral
Iron Ore Dressing. The iron ore dressing process is aimed at the processing of iron ore materials, which is divided into crushing and screening, grinding and classification, separation, and dehydration.Crushing and screening
More
Existing and New Processes for Beneficiation of Indian Iron
2020.2.8 The iron ore industries of India are expected to bring new technologies to cater to the need of the tremendous increase in demand for quality ores for steel making. With the high-grade ores depleting very fast, the focus is on the beneficiation of low-grade resources. However, most of these ores do not respond well to the conventional
More
Environmental Exam 3 Flashcards Quizlet
E) radioactive element. B) metal. 5) Smelting of iron ore involves ________. A) washing the ore with acid to extract iron. B) dissolving the ore in hot water to separate iron and aluminum. C) crushing and heating the ore at its melting point. D) oxidizing iron to ferric oxide and then adding silicon and boron.
More
Iron Ore Beneficiation Plant - JXSC Machinery - Mineral
3 天之前 Iron ore beneficiation is mainly a process of separating valuable minerals and iron minerals from ores to extract high-quality iron ore. The iron ore process mainly includes crushing, grinding, washing, beneficiation, dewatering, etc. . Magnetite Beneficiation: The main iron mineral contained in magnetite is iron tetroxide (Fe3O4). And iron in the form of
More
Ore Beneficiation - an overview ScienceDirect Topics
Life cycle assessment of iron ore mining and processing. N. Haque, T. Norgate, in Iron Ore, 2015. 20.2.5 Screening and separations. Screening is an important step for dry beneficiation of iron ore. Crushing and screening is typically the first step of iron ore beneficiation processes. In most ores, including iron ore, valuable minerals are ...
More
The six main steps of iron ore processing - Multotec
Six steps to process iron ore. 1. Screening. We recommend that you begin by screening the iron ore to separate fine particles below the crusher’s CSS before the crushing stage. A static screen is used to divert the fine particles for crushing. This step prevents overloading the crusher and increases its efficiency.
More
HEMATITE BENEFICIATION PROCESS, HEMATITE BENEFICIATION EQUIPMENT
2021.4.30 The iron ore processed by a concentrator in Inner Mongolia is a mixture of high-grade iron ore and gangue, containing 40-50% iron. After ore washing, jigging, and spiral beneficiation, a mixed ...
More
Impact of quality of iron ore lumps on sustainability of
2015.1.1 Until the early twenty-first century, iron ore mines developed in Brazil focused primarily on hematite bodies. These ore bodies typically had over 60% Fe and low levels of contaminants (such as Al 2 O 3 and SiO 2), and produced lumps (>16 mm) with physical, chemical, and metallurgical properties favorable for extraction. In the
More
Iron ore slimes beneficiation using optimised ... - ScienceDirect
2022.8.1 The iron ore slimes experiments are conducted at an operating pressure of 68.94 kPa with of 10–15% feed solids concentration in a 100 mm hydrocyclone having vortex finder of 25 mm, cone angle as 10, 12 20°
More