changing the particle size in the grinding process

Experimental and numerical investigation of particle size and particle ...
2022.9.1 The particle size after the 2nd grinding decreases further. The results also show good agreements between the simulations and the experiments for both grindings,
More
Evolution of grinding energy and particle size during dry ball
2020.10.1 The energy efficiency of dry fine grinding process of powders dramatically declines with decreasing particle size, and represents a growing concern in various
More
Grinding process particle size modeling method
Grinding process particle size modeling method using robust RVFLN-based ensemble learning doi: 10.13374/j.issn2095-9389.2019.01.007 LI De-peng 1 , DAI Wei 1, 2 , , , ZHAO Da-yong 3 , HUANG...
More
Research on Grinding Characteristics and
2022.10.26 Through the particle size analysis of the crushed products, the impact-crushing parameters A and b of the ore can be obtained. The ore is broken and divided into five particle sizes according
More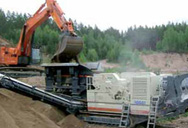
Grinding and Flotation Optimization Using Operational
2019.1.11 A novel on-line method to estimate particle size distribution shape is presented in order to improve the overall grinding and optimize the particle size shape of
More
Research on the characteristics of particles size for grinding
2021.10.1 The results show that i) finer feed size induces a significant change in the particle size of the ground products; ii) the grinding fineness of pyrite is higher given the
More
Minerals Free Full-Text Research on Grinding
2022.10.13 Introduction. Grinding is the process of reducing the particle size, which plays an important role in mining, construction, metallurgy, chemical, coal and other basic industries [ 1, 2, 3 ]. In terms
More
Effect of grinding depths on SiC nanogrinding behavior
2021.12.12 So we analyzed the whole grinding process and found that for the grinding depth of 10nm, there is no dislocation in the grinding process. For grinding depth
More
Estimation of Grinding Time for Desired Particle Size
2020.1.3 Ball mills are progressively used to grind the ores for particle size reduction and to liberate valuable minerals from the ores. The grinding of ore is a highly energy
More
Energies Free Full-Text Increasing Energy
2020.12.21 Tumbling mills have been widely implemented in many industrial sectors for the grinding of bulk materials. They have been used for decades in the production of fines and in the final stages of ore
More
Study on micro-energy consumption model of ultrafine grinding
2022.12.1 Energy consumption of coarse-grained. The fractal dimension of coarse-grained particles D3 increases slightly under the conditions of 10 min and 20 min, and remains at 2.9 after 30 min, and the value is within a range of 2.85 ± 0.05 during the whole grinding experiment. In the entire process of ultrafine grinding experiments, coal particle ...
More
Journal of Physics: Conference Series - IOPscience
From Figure 2, the results showed that low-speed grinding was a low-energy grinding process, and the distribution of product particle size was uneven, and it tended to distribute in the second coarse fractions near the original particle size of the feed itself and the fine fractions of -0.038 mm, which indicated that there were obvious abrasion ...
More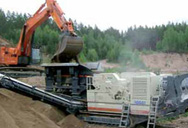
Grinding SpringerLink
2022.2.28 The particle size distribution of products from the grinding process is an essential parameter since many downstream processes such as magnetic separation, gravity separation, froth flotation, leaching, and roasting are sensitive to the particle size [4, 42]. A narrow particle size distribution is usually advantageous to improve the
More
E Process of Food Produce: A Review - mdpi-res
2020.3.20 required during the process and an increase in powder product yield has been reported [7]. Therefore, before the dry grinding process, the unit operation of drying must be ensured to have properties that will enhance the grinding unit operation. Grinding as a unit operation is widely used in the food industry and designed to reduce the size
More
Full article: Potentials of superfine grinding in quality
2023.8.29 Superfine grinding is an emerging technology that reduces particle size and modifies surface properties (Hu et al., Citation 2012).It is a novel processing method that is capable of degrading the organization of plant materials and thereby modifying the performance and the release of nutrients (Gao et al., Citation 2020a). To boost the use of
More
Particle Size Matters - Chemical Engineering Page 1
2020.1.1 Particle sizing is an essential task in the chemical process industries (CPI) where achieving high-quality product efficiently and at a low cost is the name of the game. For this reason, appropriate size-reduction equipment is critical to overcoming process challenges that impede throughput, as well as acing new applications that require ...
More
Material Removal Mechanism and Force Modeling in
2023.10.27 With the development of medical engineering technology, micro-trauma and rehabilitation have become one of the development directions of surgery [1, 2], and micro-grinding of bone materials has become a hot topic of scholars [3,4,5,6].Micro-scale grinding mainly refers to the direct mechanical removal process using a micro-abrasive
More
Importance and optimization of particle size in animal feed
2022.3.9 The figure underneath shows the relation between the average particle size and the Hammer Mill tip speed. When changing speed with a frequency controller on a 3,2 mm screen you achieve a grind of 500-600 micron at 127 m/s, while when grinding on only 76 m/s the average particle size is 700-800 micron.
More
Grinding process particle size modeling method using robust
As a key production quality index of grinding process, particle size is of great importance to closed-loop optimization and control. This is because controlling particle within a proper range can improve the concentrate grade, enhance the recovery rate of useful minerals, and reduce the loss of metal in the sorting operation; thus, the particle size determines the
More
The effect of bean origin and temperature on grinding
2016.4.18 Figure 3: Upper panel: The particle size distribution as a function of number (cumulative) of physical particles (shown in blue) and the integral of this data (shown in grey), yields 99% of the ...
More
Roller mills: Precisely reducing particle size with greater
2020.11.11 Ground particles discharged by gravity from bottom roll pair’s roll gap. More about the rolls. Common roll diameters are from 6 to 10 inches, and roll lengths — which vary with the roll diameter to ensure that the roll will be mechanically robust — are from 8 to 52 inches. Longer rolls provide greater grinding capacity.
More
Materials Free Full-Text Effect of Size-Distribution
2023.12.17 The so-called population balance model (PBM) is the most widely used approach to describe the grinding process. The analysis of the grinding data is carried out using—among others—the one-size fraction BII method. According to the BII method, the breakage parameters can be determined when a narrow particle size fraction is used as
More
Study on the Effects of Grinding Factor and Scaling up in
relationship with particle size can be controlled by specific energy when bead mill in liquid phase (wet grinding) is used. Combined with the result of this experiment, pulverizing process can also be optimized in consideration of combining wet and dry bead mill. Figure 4. Relationship between the specific energy and particle size in each bead ...
More
Particle Size Reduction Techniques of Pharmaceutical
2021.1.11 A few other terms such as grinding, comminution, and pulverization are interchangeably used for the milling process. ... They reported that the average particle size varied between 0.36 and 8.1 µm by changing the carbon dioxide bubbling rate over about two orders of magnitude. The low and high anti-solvent bubbling rates lead to narrow and ...
More
A process mineralogy approach to study the efficiency of
2020.12.3 According to the PSD diagram shown in Fig. 5 as well as Table 1, the grinding process in open-circuit mill produces about 70.0% of the fine product with particle size smaller than 20.0 microns; of ...
More
Effect of mechanical grinding time on the particle groups ...
2023.4.1 The characteristic sizes (D90, D50 and D10) could comprehensively reflect the variations in particle size during mechanical grinding. In this study, the relative reduction degree (R) of YRS particle size was used to quantitatively characterize the decreasing degree of YRS particle size after mechanical grinding, as expressed in equation (1) [31].
More
Grinding (Comminution) - an overview ScienceDirect Topics
During the grinding process, the nanopore structure of coal has been modified significantly, suggesting that the mechanical force has an evident effect on changing the original pore structure of coal. As the particle size reduces, the sample pore volume per
More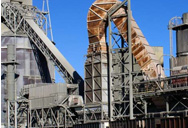
The Science Behind Coffee Extraction: How Grind Size
2022.12.21 In addition to faster extraction times, a finer grind causes water to pass through more slowly. Water will pass through faster with a coarser grind, making extraction much easier. Furthermore, the size of the grind affects the flavor of the coffee because the time between the water and the grind can be short or long.
More
Online monitoring and control of particle size in the grinding process ...
2015.5.1 The product particle size in a cement mill is a non-linear function of the mill inputs [26] and because of this non-linearity, accurate mathematical modeling of the cement grinding process is highly difficult. Therefore, data based approach has been adopted in this work for grinding process modeling.
More
Nanoparticles: Building Blocks for Nanotechnology
The small particle size leads to many unique properties of nanoparticles. ... To avoid particle aggregation in the course of the size reduction process, the grinding and milling operations are often carried out with colloidal stabilizers. Nagarajan and Hatton; Nanoparticles: Synthesis, Stabilization, Passivation, and Functionalization ...
More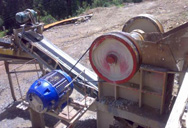
Effect of Moisture Content on the Grinding Process and
2018.4.28 Grinding is a staple size-reduction process to produce food powders in which the powdered form is chemically and microbiologically stable and convenient to use as end products or intermediate products. The moisture content of food materials before grinding is a particularly important factor, since it determines the materials’ physical
More
METHODS OF SIZE REDUCTION AND FACTORS AFFECTING SIZE
2013.9.9 Technical analysis reaffirm that Kick's equation could only achieve coarse particles as the final particle size showed average percentage deviation of 38.40%, while Bond's equation may be limited ...
More
Study of the parameters influencing the co-grinding process
2011.9.15 Co-grinding is a procedure for the preparation of nanoparticles in which the drug is ground together with one or more excipients. The grinding of meloxicam, a crystalline solid, together with amorphous polyvinylpyrrolidone (PVP) or semi-crystalline polyethylene glycol (PEG) as excipients, is expected to lead to a drastic reduction in particle size.
More
Dynamics of fine grinding in a fluidized bed opposed jet mill
2018.3.1 Abstract. Today the modeling of the process dynamics and the complex two-phase flows in mills still remain a challenging task. In this study the dynamic comminution process in a fluidized bed opposed jet mill is investigated. For this purpose, well-defined model glass beads were ground in a lab-scale mill. The particle size
More
Mechanical activation of steel slag to prepare supplementary ...
2022.11.15 Irrespective of the grinding conditions (grinding process and grinding time), the steel slag particle sizes consistently exceed 0.46 μm. In other words, the particle sizes of steel slag particles do not further decrease with an increase in grinding time or a change in grinding process; this is attributable to the intensive interaction between ...
More
Production of powder coatings with defined particle size
2004.12.10 The optical and functional properties of powder coatings depend on the particle size distribution of the powder. The production steps for powder paint are mixing and extrusion of the raw material, cooling, pre-crushing and grinding. Depending on the requirements, the ground material is either collected in a cyclone or an inline classifier.
More
Size Reduction SpringerLink
2022.3.23 Size reduction is a process in which particles with smaller size and large surface areas are formed, which ultimately eases the processing. The chapter explains the size reduction mechanism during compression, impact, cutting, shearing, and attrition. The stress-strain behavior of materials during mechanical failure also plays an important role ...
More
Impact of the Drying Temperature and Grinding Technique on
2020.7.2 The process of biomass compaction depends on many factors, related to material and process. One of the most important is the proper fragmentation of the raw material. In most cases, more fragmented raw material makes it easier to achieve the desired quality parameters of pellets or briquettes. While the chipping of biomass prefers
More