cone crusher purpose

A Detailed Overview of Cone Crushers and What
2020.6.3 Usually, these crushers deliver a 4:1, 5:1, or 6:1 reduction ratio. As you reduce the closed side setting to produce smaller material,
More
Cone Crusher SpringerLink
2023.5.3 Cone crusher is a type of crushing equipment whose crushing cone rotates in the conical cavity within the shell to realize intermediate crushing or fine crushing of
More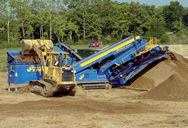
What Is a Cone Crusher and What Can It Do for You?
2021.1.10 A cone crusher is one of many different types of crushers, like impact crushers, jaw crushers, and hammermills, that is used to process and reduce material
More
How Does A Cone Crusher Work: Understanding The
2023.7.31 The primary purpose of a cone crusher is to reduce the size of big rocks into smaller ones. The whole process is achieved through a series of stages in the cone
More
Cone crusher basics in 4 minutes - rockprocessing.sandvik
Cone crusher basics in 4 minutes This is the starting point for understanding how cone crushers work – and how they can make your mine or quarry more productive.
More
CONE - Chalmers Publication Library (CPL)
2022.11.25 Cone crushers are used by both aggregate producers and the mining industry. The purpose of using crushers is to reduce the particle size of rock materials or
More
REAL-TIME OPTIMIZATION OF CONE CRUSHERS - CORE
2017.11.22 Cone crushers are used in the mineral, mining, and aggregate industry for fragmentation and production of rock materials. Cone crusher control systems are widely
More
Analysis of cone crusher performance with changes in
2017.1.1 Cone crusher designs and power trains are usually optimised for aggregate crushing as their main use is traditionally for production of aggregate. Ores which are
More
How Does A Cone Crusher Work: Understanding The
2023.7.31 The cone crusher has a high reduction ratio, ensuring efficient material crushing. Discharge: This is the final stage of the crushing process. When the material is crushed into the preferred size, it exits the cone crusher through an opening at the bottom. The entrance is located between the mantle and the bowl liner.
More
SANDVIK CH870 CONE CRUSHER - Sandvik Mining and
2017.9.15 Purpose Supplies oil to the crusher and pinionshaft lubrication systems and to the Hydroset system Control system The crusher lubrication system is monitored by the Tank Instrumentation Monitoring System (TIMS) No. of doors 4 No. of inspection hatches 3 located on top of unit Cabinet material Metal Dimensions (LxWxH) 3,106 x 1,401 x
More
Understanding the Cone Crusher Working
2023.2.23 The cone crusher working principle involves the eccentric motion of the main shaft. This motion is created by the rotation of the main shaft, which is supported by a bearing located at the top of the machine.
More
Crushers - All crusher types for your reduction needs - Metso
Cone crushers can in most cases also give a good cubic shape to fine grades. They can be adapted to different applications. This is an important factor, as client-specific needs often change during a crusher’s lifetime. For cone crushers there are few rules to be followed of optimum cubical shape. These ‘Ten Golden Rules’ are:
More
Fast and safe removal of wear parts Crusher wears lifting
2023.8.2 Efficient crusher maintenance Specially designed, fit-for-purpose tools makes wear part change-outs faster and more efficient. By using OEM parts, risk of damaging equipment is avoided. As a result, maintenance times are shortened and crusher downtime is reduced. Improved safety and quality To succeed in today’s competitive
More
A fundamental model of an industrial-scale jaw crusher
2017.5.1 Abstract. In this study, an analytical perspective is used to develop a fundamental model of a jaw crusher. Previously, jaw crushers were modelled in regard to certain aspects, for example, energy consumption (Legendre and Zevenhoven, 2014) or kinematics (Oduori et al., 2015). Approaches to date have been mainly property specific.
More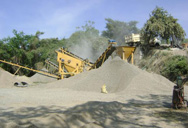
Chamber Optimization for Comprehensive Improvement of Cone Crusher ...
2021.3.15 This study aims to analyze the impact of key structural parameters such as the bottom angle of the mantle, the length of the parallel zone, and the eccentric angle on the productivity and product quality of the cone crusher and optimize the crushing chamber to improve the crusher performance. The amount of ore in the blockage layer was
More
The Complete Guide to Primary Crushing, Secondary
2023.2.28 Primary, secondary, and tertiary crushing are three stages in the comminution process that break down large rocks into smaller pieces of varying sizes. Each stage uses different types of crushers and has distinct advantages and disadvantages. This article provides a comprehensive guide to primary, secondary, and tertiary crushing.
More
Replacing the liner of a HP cone crusher - Metso
2017.6.9 A) Mantle - also known as head liner. B) Cutting ring - the cutting ring is not reusable, so a new ring should be installed every time the mantle is replaced. C) Bowl liner. D) Padding material - its purpose is to cushion (shock absorption), not to fasten the liners. Lubrication of the head/bowl is recommended to facilitate subsequent replacement.
More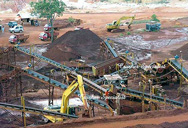
EP0093069A2 - Anti-spin device for cone crusher - Google
An anti-spin device for a cone crusher having a stationary spindle (62) and a gyrating crusher head (36) driven by an eccentric (20) and running within a stationary crusher bowl (48), said anti-spin device comprising: an elastomeric body (80) fastened to one of said spindle and said crusher head; a member (70) fixed to the other of said spindle ...
More
Crushing 101 – Different types of crushers for distinctive needs
2020.12.17 Jaw crushers can be divided into two basic types, single and double toggle. In the single toggle jaw crusher, an eccentric shaft is on the top of the crusher. Shaft rotation, along with the toggle plate, causes a compressive action. A double toggle crusher has two shafts and two toggle plates. The first shaft is a pivoting shaft on the top of ...
More
Types of Crushers: What You Need to Know - Machinery
Cone crushers are one of the main choices for secondary crushing. A cone crusher is a powerful machine that is used in large-scale industries for crushing various types of materials into smaller sizes. It works by applying pressure onto the material and squeezing it against a rotating mantle to create compression and force. The crushed material ...
More
Crusher - an overview ScienceDirect Topics
The cone crusher is a modified gyratory crusher. The essential difference is that the shorter spindle of the cone crusher is not suspended, as in the gyratory, but is supported in a curved, universal bearing below the gyratory head or cone (Figure 8.2). Power is transmitted from the source to the countershaft to a V-belt or direct drive.
More
An experimental investigation on rock crushability using jaw and cone ...
2019.4.18 Abstract and Figures. This study covers the investigation of rock crushability using laboratory-scale cone and jaw crushers for five types of hardrocks. For this purpose, physico-mechanical ...
More
CONE - Chalmers Publication Library (CPL)
2022.11.25 The purpose of using crushers is to reduce the particle size of rock materials or to liberate valuable minerals from ores. A tremendous amount of material is crushed yearly by cone crushers. Despite this fact, the detailed knowledge of how a cone crusher works from a process point of view is quite poor.
More
Cone crusher modelling and simulation using DEM
2016.1.1 Abstract. Compressive crushing has been proven to be one of the most energy efficient principles for breaking rock particles (Schönert, 1979). In this paper the cone crusher, which utilizes this mechanism, is investigated using the discrete element method (DEM) and industrial scale experiments. The purpose of the work is to develop a virtual ...
More
Maximize your cone crusher productivity Pit Quarry
2017.4.28 Providing better crusher feed control for the cone crusher through the use of surge piles, hoppers and variable-speed feeding devices such as belt conveyors or vibrating pan feeders can easily increase crusher productivity by a minimum of 10 percent. Metso’s Lokotrack LT220D combines a crusher and screen onto the same chassis.
More
Gyratory Crusher SpringerLink
2023.5.11 Gyratory crusher is a crushing equipment that uses the gyratory motion of the crushing cone in the conical cavity inside the shell to extrude, bend, and impact materials, for the purpose of coarse crushing of the materials of various hardness. It was invented in the USA in the 1870s. The equipment specification is usually represented by
More
Control oriented modeling of flow and size distribution in cone ...
2014.2.1 Changing CSS and ω on-line may give a significant improvement in crusher operation, and suggestions of control algorithms utilizing this possibility have begun to emerge (Hulthén and Evertsson, 2011, Hulthén, 2010).The purpose of this paper is to formulate a process model for developing and simulating closed-loop strategies by using
More
Size reduction control in cone crushers - ScienceDirect
2021.11.1 Fig. 3 illustrates the operating principle and the main components of a cone crusher. A cone crusher basically comprises two bell-shaped manganese crushing liners placed inside each other. The concave is attached to the crusher frame and the mantle to the eccentric main shaft which is swaying around the geometric center point at the
More
Forces in a Cone Crusher Steel in Translation - Springer
2019.3.21 The crusher will be most effective when the mobile cone rotates around its axis. In that case, force Fro acts on the piece, creating an internal torque. Such behavior is feasible within a cone crusher with parallel axes of the crusher and the mobile cone, if the mobile cone is rigidly attached to its shaft.
More
Evaluation of size reduction process for rock aggregates in cone crusher
2020.6.4 The size reduction process of rocks in cone crushers is one of the most important issues, particularly for the secondary and tertiary stages of crushing operations. In this study, 17 different rock types were considered for the evaluation of their size reduction variations that occurred in a laboratory-scale cone crusher. Based on several
More
MVPX Series Cone Crushers - Terex
2021.4.21 Cone Crushers Static MVPX Technology Advantages/Key Features • New ACE8 Advanced Automated Cone Control System helps improve the crusher’s performance as well as overall reliability, including a bowl float monitoring system as standard. • Fully guided dual action tramp relief cylinders provide 6” (152 mm) lift for easy clearing of
More
Research on the Wear Behavior of the Fixed Cone Liner of a Cone Crusher ...
Taking reducing the wear of the fixed cone liner of a cone crusher as the starting point, the movement and geometry parameters of the cone crusher are studied using the discrete element method. To improve the service life and working efficiency of the whole cone crusher. The UG model and discrete element Yade model of the cone crusher are
More
Sandvik Cone Crushers - SRP
Sandvik cone crushers are an excellent choice in secondary, tertiary, quaternary and pebble-crushing applications. They are equipped with the hydraulic Hydroset™ system, which provides safety and setting-adjustment functions. Our crusher automation system delivers real-time performance management, enabling you to monitor and optimize
More
Breakage process of mineral processing comminution
2020.9.1 However, in mineral processing, it is not common to reach this low level of rate. For instance, Evertsson introduced cone crushers as a compressing crusher in which the rock is broken by squeezing between two surfaces [33]. He calculated the working velocity in a specific type of cone crusher at choke-level from 0.5 to 1 m/s.
More
CS840i - SRP
It’s 90% faster to change liners compared to welding. The improved over-pressure system with dedicated air channel inlets keeps dust out to increase reliability. The standard off-line filter unit keeps the lubrication oil cleaner with 24/7 fine filtration, reducing wear on your internal crusher components and extending oil life by up to 5 times.
More
Jaw Crusher Explained - saVRee
Purpose of Material Crushers (Size Reduction) A crusher is a machine designed to reduce the size of large rocks to smaller rocks , gravel , sand, or rock dust; this is essential for efficient transport of the product via conveyors etc. Crushing is the first of many stages that lead to separation of the mineral (s) from the waste ( gangue ...
More
(PDF) COMPARISON OF SECONDARY CRUSHING OPERATIONS THROUGH CONE
2020.9.20 The purpose of this research is to develop an automated control system for Jaw crusher production process as a solution for the real specified problems to get more productive aggregate production.
More
Reliability centered maintenance of cone crusher: a case
2017.8.24 Abstract A cone crusher is used for crushing rock. The vast majority of these installations are found in mineral processing plants. The Reliability of the crusher influences the productivity of the plant. The purpose of this paper is to focus the application of reliability centered maintenance with an aim to improve the reliability of the cone ...
More