replacing coke with pulverized coal new steel

Comparison of semi-coke with traditional pulverized coal
2022.1.11 In this work, 46 types of semi-coked prepared via low-rank coal pyrolysis in the Shenmu area of Northwest China are researched, and coal with different ranks for PCI and coke breeze are used as comparison samples to explore the theoretical feasibility of
More
To what extent could biochar replace coal and coke in steel
2023.5.1 In fact, addition of 2 to 10 % biochar to the coal blend, reduces 1–5 % of CO 2 emission in the steel industry which it values 0.02–0.11 ton CO 2/ton crude steel [31].
More
(PDF) Replacement of Pulverised Coal Injection (PCI
2021.11.10 This paper describes the present status of coal utilization in ironmaking two main processes of coal injection into blast furnace developed to save expensive
More
Thermal analysis and kinetic modeling of pulverized coal
2021.4.13 Comparing the combustion characteristics and kinetic parameters of mixed fuels with different coke breeze contents, it is acceptable to use a small amount of coke
More
Coal Combustion Behavior in New Ironmaking Process of
The pulverized coal injection (PCI) is pursued to reduce the hot metal production cost by replacing the expensive metallurgical coke with the non-coking coal. Increasing the PCI
More
Partial substitution of coke breeze with biomass and
2020.10.15 In the present study, sintering was carried out with variable proportions of biomass and coke to seek out the optimum quantity of biomass that could effectively
More
Meeting a burning need for cleaner steelmaking
2020.8.27 The use of near 100% pure oxygen helps enhance the combustion reaction of pulverized coal, which is conducive to reducing coke consumption.
More
Co-combustion of semicoke and coal in an industry
2019.12.15 Pulverized Coal Injection (PCI) is an important standard technology replacing coke partially by pulverized coal into the blast furnace that allows a significant
More
Effect of Coal and Coke Ash on Blast Furnace Slag Properties:
2021.5.13 The global trend is to decrease the use of fossil-based carbon by replacing it with bio-based coal. Ash from coke and pulverized coal eventually dissolve in the final
More
Energy Conservation and CO2 Abatement
This paper mainly focuses on the energy conservation and CO 2 abatement potential of a gas-injection BF using carbon consumption curves. In addition, three scenarios, i.e ., a traditional all-coke BF, traditional PCI BF and gas
More
Effect of hydrogen addition on reduction behavior of iron
2017.2.10 Therefore, understanding the impacts of new reaction conditions on coke rate and quality requirements is important to both coal producers and steel manufacturers. This paper reviews the current understanding of how the introduction of alternative reducing agents into the blast furnace influences the gasification behavior, degradation mechanism ...
More
Study on the Combustion Performance and
2023.5.20 In this study, the feasibility indicators of the injection of coke breeze for blast furnaces (BFs) were tested. Experiments were conducted on the combustion behavior of coke breeze at different
More
Use of PCI in blast furnaces - ICSC
2018.2.2 Pulverised coal injection (PCI) provides important economic and operational benefits. These include: lower consumption of expensive coking coals. Replacing coke with cheaper soft coking or thermal coals reduces reductant costs. It takes about 1.4 t of coking coal to make 1 t of coke, which can be replaced by 1 t of pulverised injected coal ...
More
A Numerical Study of Scenarios for the Substitution of
2023.5.10 Increasing the pulverized coal injection to the desired level is a complicated matter for blast furnace technology. The main causes are the furnace’s gas flow management and an accumulation of unburned coal particles at the bottom section of the furnace, which can produce unstable solid and liquid descending motions [4,8,10–16 ...
More
The future of steelmaking - Roland Berger
2023.12.22 Methods such as coke dry quenching and optimizing pellet ratios, as well as BF equipment like top gas recovery turbines, reduce conventional primary route carbon emissions. Replacing coke with natural gas can also significantly cut CO 2 in primary steelmaking, as can injecting hydrogen or ammonia into the BF to partly replace
More
Thermal analysis and kinetic modeling of pulverized coal
2021.7.1 Results showed that with the increase in coke breeze addition from 15% to 60%, the indexes C and S decrease, and the activation energy of the first stage remains almost constant, while that of the last stage increases from 16.89 up to 67.18 kJ mol-1, which indicates that adding coke breeze decreases the combustion efficiency of
More
Low-carbon production of iron and steel: Technology
2021.3.9 show that using H 2 as an auxiliary reducing gas for BF to partly replace CO derived from either coal or coke can reduce CO 2 emission by 21.4%. Pure H 2 injection into the BF by tuyeres through its raceway at the bottom of the BF, replacing 120 kg/t pulverized coal (PC) with 27.5 kg/t heated H 2 injection.
More
Low-Carbon Production of Iron Steel: Technology Options
2021.3.8 Yilmaz et al. [(Yilmaz et al., 2017)] show that using H2 as an auxiliary reducing gas for BF to partly replace CO derived from either coal or coke can reduce CO2 emission by 21.4%. Pure H2 injection into the BF by tuyeres through its raceway at the bottom of the BF, replacing 120 kg/t pulverized coal with 27.5 kg/t heated H2 injection.
More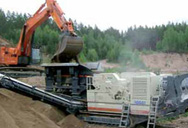
Use of Waste Plastics in Coke Oven: A Review - Springer
2017.8.25 substitute reducing agent for coke and pulverized coal in a blast furnace to produce pig iron [3–5]. Pig iron is pro-duced in a blast furnace by melting and reducing iron ore by use of coke. Waste plastics composed of carbon and S. Nomura () Ironmaking Research Laboratory, Process Research Laboratories, Nippon Steel Sumitomo Metal
More
(PDF) Technological advancements in evaluating the performance
2020.9.11 Schematic of pulverized coal injection in the lower part (lance-blowpipe-tuyere-raceway-coke bed) of a BF [49]. Effect of lance location on the combustion efficiency and ash deposit [51]. +9
More
Partial substitution of coke breeze with biomass and
2020.10.15 It succeeded in replacing coke by 10% of sawdust, 30% of wood charcoal, and 30% by a combination of sawdust and charcoal. ... /t crude steel, and the reduction potential reached 66.94% mostly. Among all the steel production processes, Blast furnace in BF-BOF route had the largest emission contribution proportion (72.06%),
More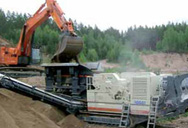
Effect of Coal and Coke Ash on Blast Furnace Slag
2021.3.29 metallurgical coke and pulverized coal, and changes in thefinal slag compo-sitions and properties are focused on. The global trend is to decrease the use of fossil-based carbon by replacing it with bio-based coal. Ash from coke and pulverized coal eventually dissolve in thefinal slag, affecting its properties. The
More
Coal Combustion Behavior in New Ironmaking Process of
The top gas recycling oxygen blast furnace (TGR-OBF) is a new ironmaking process which can significantly reduce the coke ratio and emissions of carbon dioxide. To better understand the coal combustion characteristics in the TGR-OBF, a three dimensional model was developed to simulate the lance–blowpipe–tuyere–raceway of a TGR-OBF. The
More
Effect of coaxial oxygen enrichment on three different coals
2021.3.1 Replacing coke is important because it has a higher price than coal, and a large amount of COG is released during its production (coke oven gas) . The injection of pulverized coal was intensified around 1980, during this time, other fossil fuels were also used to be injected as alternative fuels, but coal presented the lowest price and the most ...
More
Use of Hydrogen–Rich Gas in Blast Furnace Ironmaking of
2022.9.1 When only pulverized coal is injected, the RAFT is 2230.3 °C. As each of the three hydrogen–rich gases replaces part of the coke and starts injection, the RAFT decreases at a slower rate with the increase in the injection quantity. However, the effect of different hydrogen–rich gases’ injection on the RAFT is obviously different.
More
Thermal analysis and kinetic modeling of pulverized coal
2021.4.13 Pulverized coal injection technique has been widely used as a means of reducing coke consumption during ironmaking process. Owing to the increasing shortage of fossil fuels, other substitutes such as biomass, plastic, and waste tires have been studied in recent years. Coke breeze as one of the by-products of coking industries has been
More
The Effect of Bio-Coal Agglomeration and High-Fluidity Coking Coal
2023.1.15 Metallurgical coke with high strength and low reactivity is used in the ironmaking blast furnace. Replacement of some coking coal with bio-coal was shown to result in lower strength and higher reactivity of produced coke due to introduction of reactive bio-coal carbon and ash components catalyzing the Boudouard reaction, but also due to
More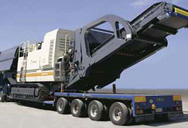
A Numerical Study of Scenarios for the Substitution of Pulverized Coal ...
2023.5.10 A numerical simulation procedure is proposed for analyzing the partial replacement of pulverized coal injection by hydrogen, oxygen, and blast furnace gas (BFG) injections mixed with pulverized coal (PCI) within the tuyeres of large blast furnaces. The massive use of hydrogen-rich gas is extremely interesting for ironmaking blast furnaces
More
Sustainability in steelmaking - ScienceDirect
2020.8.1 Review articleSustainability in steelmaking. Sustainability in steelmaking. The steelmaking industry relies on fossil fuel sources such as coal and coke (around 70% of the total energy required) to supply the increasing demand for steel (nearly 1752 million tones for 2020), which has an extreme impact on the environment, releasing almost 27%
More
Sustainable development of primary steelmaking under
2015.6.16 New concepts studied are blast furnace operation with different degrees of top gas recycling and oxygen enrichment of the blast to full oxygen blast furnace. ... Another way to suppress harmful emissions from the steelmaking sector is by replacing coke with other carbon and hydrogen carriers, such as pulverized coal, oil, natural gas, biomass ...
More
Effects of hydrogen fraction in co-injection gas on
2023.4.8 In addition, the burnout rate of pulverized coal increases benefited from the oxygen blast, which provides further increase space for the coal ratio and then the coke ratio can be reduced. In the second technical route, hydrogen-rich gas, such as natural gas, coke oven gas, coal pyrolysis gas and ... which become a new trend for the development ...
More
Using SPL (Spent Pot-Lining) as an Alternative Fuel in
2016.5.31 Replacing coke (coal) in a metallurgical furnace with other alternative fuels is beneficial for process economics and environmental friendliness. Coal injection is a common practice in blast furnace ironmaking, and spent pot-lining (SPL) was conceptualized as an alternative to coal. SPL is a resourceful waste from primary Aluminum production,
More
PCI coal for steelmaking soon to be impacted by
2022.5.10 PCI coal will be the first grade of metallurgical coal impacted by the decarbonisation of steel. 10 May 2022 (IEEFA): Steel-making companies are exploring replacing Australia and Russia’s increasingly expensive and supply-challenged PCI coal with green hydrogen as an early pathway to reducing emissions in the steel industry, finds a
More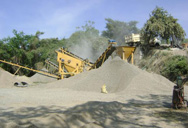
Numerical simulation study on the effects of co-injection of pulverized ...
2023.12.15 Section snippets Model description. After being transported through the gas pipeline, the MF enters the tuyere and undergoes energy and momentum exchange with the high-temperature hot air, generating CO, CO 2, and other substances during combustion.The simulation mainly focuses on the following aspects: (1) turbulent
More
The Application of Lignocellulosic Biomass Waste in the Iron and Steel ...
2023.9.17 Coal and coke are fossil fuels that serve as the iron and steel industry’s primary energy sources. One of the potential methods to minimize the use of fossil fuels and to reduce CO 2 emissions is the partial replacement of coke and coal in blast furnaces with biomass. Products made from biomass can be used in place of fossil carbon for ...
More
Study on Combustion Characteristics and Kinetics of Coal and Semi-Coke ...
2023.9.13 Abstract The combustion behaviors of semi-coke, anthracite, bituminous coal and their blends were studied using a thermogravimetric analyzer. Compared with anthracite, the experiments showed that semi-coke had low ignition temperature, good comprehensive combustion characteristics and high burnout rate. In compound samples,
More
Industrial uses of coal - ScienceDirect
2013.1.1 The ironmaking process, including coke plant and sinter plant, consumes 56–75% of the total energy at an integrated steel works. New processes to potentially reduce the costs of both coal and iron for ironmaking by the traditional blast furnace route have been going on for many years, and they include the development of processes
More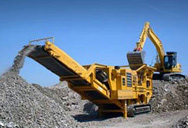
Processes Free Full-Text Combustion Enhancement of Pulverized Coal ...
2021.2.28 The coke involved in this process must be used during the blast furnace production process and about 350 kg of coke will be consumed for a tonne of hot metal. ... there is a need to develop a new blast furnace pulverized coal injection technology. ... She, X.; Wang, J. Effect of Oxygen-Coal Lance Configurations on Coal Combustion Behavior ...
More
Modern technological route of converter production of
Based on the results of a comparative analysis of the structure of technological routes for the production of iron-carbon semiproducts at metallurgical enterprises in Ukraine and abroad, it is shown that it is advisable to use blast furnace technology at Ukrainian enterprises by partially replacing coke with pulverized coal, involving ...
More
Modelling the injection of upgraded brown coals in an
2017.6.1 Victorian brown coal is a low-cost and abundant resource, featuring in high moisture and low ash yield, and has a potential of replacing high grade metallurgical coals in pulverized coal injection (PCI) in ironmaking blast furnace (BF). In this paper, a three-dimensional mathematical model is used to simulate the flow and thermochemical
More