feo reduction method in magnetite iron ore concentrate
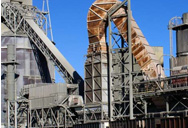
Original Research PaperMechanism of magnetite iron ore
2022.12.1 Abstract. The effect and mechanism of magnetite concentrate morphology on the quality of indurated pellets were investigated. Concentrates with different morphologies were prepared using high-pressure grinding rolls (HPGR) and ball mill
More
The Efficient Improvement of Original Magnetite in Iron Ore Reduction ...
2021.6.17 Magnetization roasting followed by magnetic separation is considered an effective method for recovering iron minerals. As hematite and magnetite are the main
More
Optimization of FeO in iron ore pellet with varying blend of hematite ...
2015.10.24 Request PDF Optimization of FeO in iron ore pellet with varying blend of hematite and magnetite Ore Magnetite and hematite concentrates are the two main iron
More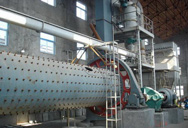
Making Iron Directly From Concentrate by Gaseous
2023.10.19 reduction of iron ore concentrate (MBIT). These technologies are designed to produce iron directly from iron concentrate without requiring
More
Improved iron recovery from low-grade iron ore by efficient
2022.8.1 RF and SRM processes were used to separate low-grad iron ore after pre-concentration. • After magnetization roasting, most hematite in the ore was reduced to
More
Mechanism of magnetite iron ore concentrate morphology
2022.12.1 Iron ore pelletizing is a two-step process. This begins with the formation of green pellets with the addition of a binder to improve agglomeration phenomena. Then it
More
(PDF) Iron Ore Concentrate - Oxidation and Reduction
1994.10.1 Different prereduction rates of oxidized magnetite concentrates are explained by characterization of raw material. Oxidation of magnetite Some Sydvaranger
More
Fluidized magnetization roasting of refractory siderite-containing iron ...
2023.4.18 Magnetization roasting is one of the most effective way of utilizing low-grade refractory iron ore. However, the reduction roasting of siderite (FeCO 3) generates
More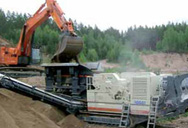
Surface Morphology and Structural Evolution of Magnetite-Based Iron Ore ...
2022.3.23 The use of magnetite-based iron ore fines by means of fluidized bed technology has become a promising route to produce direct reduced iron. The significant
More
The Efficient Improvement of Original Magnetite
2021.6.17 Magnetization roasting followed by magnetic separation is considered an effective method for recovering iron minerals. As hematite and magnetite are the main concomitant constituents in...
More
Parameter Optimization for Hydrogen-Induced Fluidized Bed Reduction
2023.2.8 Hydrogen-based direct reduced iron (HyDRI) produced by fluidized bed has great potential for achieving the target of net-zero carbon in steelmaking. However, when magnetite ores were used as feedstock, several process parameters showed influences on its fluidization and reduction behaviors. To confirm the dominant influencing factors and
More
Clean iron production through direct reduction of mineral iron ...
2021.12.1 The state-of-the-art procedure for processing iron ore is based on the reduction of mineral iron oxide (mainly hematite, Fe 2 O 3) in the blast furnace (Eq. (1)). This process emits 1.8–2.0 t CO 2 t −1 steel when carbon (coke) is used as reducing agent and energy source (Ariyama et al., 2019). 1 1 2 Fe 2 O 3 + 3 2 CO ⇌ Fe + 3 2 CO 2
More
Review on the Oxidation Behaviors and Kinetics of
2021.4.21 The available ores are becoming much more expensive and the quality is decreasing. The global production of magnetite iron ore in 2015 is 583 million tons, which accounts for 28% of the total iron ore
More
Determination method of high-temperature characteristics of iron-ore ...
2019.1.30 The high-temperature characteristics of iron ores play important roles in optimizing ore proportion of sintering, which are tested by using iron-ore fines and analytical reagent CaO as raw materials. Two calculation methods of CaO addition amount based on binary basicity (basicity method) and n(Fe2O3)/n(CaO) (mole ratio method), respectively,
More
Mechanism of magnetite iron ore concentrate morphology
2022.12.1 The chemical composition of magnetite concentrate and bentonite are presented in Table 1. It can be found that 82 wt% of the iron ore concentrate is composed of magnetite and 11 wt% of hematite, while SiO 2, MgO, CaO, and Al 2 O 3 are present as the main gangues in iron ore concentrate. Total Fe agrees well with reported values in
More
Mechanisms in oxidation and sintering of magnetite iron ore
2008.4.9 Thermal volume changes and oxidation mechanisms in magnetite iron ore green pellets balled with 0.5% bentonite binder, as a function of raw material fineness and pellet porosity, are shown. When a pellet starts to oxidize, a shell of hematite is formed around the pellet while the core still is magnetite. Dilatation curves were measured under
More
Preparation of reduced iron powder for powder metallurgy from magnetite ...
2021.11.1 The magnetite concentrate used in this study was collected from an ore dressing plant in China; its chemical composition is listed in Table 1.As can be seen from Table 1, the primary element was Fe, and the grade of iron was 64.86%, which is much lower than that of high-purity magnetite and iron scale.The predominant impurity was SiO
More
High-Efficiency Smelting Separation of Vanadium–Titanium Magnetite
2023.7.17 South African vanadium–titanium magnetite is a complex mineral resource rich in iron, vanadium, titanium, and chromium [1,2,3].Its ore composition is composed of more than 20 elements [4,5,6].It is the most complex ore of its type in the world and contains more than 10 valuable elements, so it has a very important integrated utilization value.
More
(PDF) Mineral and Technological Features of Magnetite
2021.3.24 Mineralogical studies have established that the main iron-bearing mineral is hematite, which contains 69.02 to 70.35% of iron distributed in the ore. Magnetite and hydrogoethite account for 16.71 ...
More
Minerals Free Full-Text Clean Utilization of Limonite Ore
2022.2.17 As a typical refractory iron ore, the utilization of limonite ore with conventional mineral processing methods has great limitations. In this study, suspension magnetization roasting technology was developed and utilized to recover limonite ore. The influences of roasting temperature, roasting time, and reducing gas concentration on the
More
Recovery of iron from iron tailings by suspension
2023.2.1 The temperature was 800 °C, the roasting time was 60 min, and the amount of coconut shell was 20 %. Iron concentrate which iron grade is 63.2 % was recovered from iron ore which iron grade is 49.02 %, and the iron recovery rate was 66.2 % (Nayak et al., 2019). In this study, Under the conditions of a fast pyrolysis temperature of 700 °C, SMR ...
More
An Efficient Process to Recover Iron from Bayer Red Mud
2022.6.15 Previous studies on the efficient recovery of fine-grained iron minerals from red mud have mainly focused on the method of reduction roasting and magnetic separation; that is, iron oxides are reduced to magnetite or iron elements by strong magnetism, and iron concentrate can be obtained by magnetic separation of the roasted ore. 9 In addition ...
More
Mineralization characteristics of pellets prepared by ultrafine ...
2022.10.25 The reducing property of pellets prepared by ultrafine magnetite concentrate (UMC) and improving method were revealed. The results show that the reduction degree of UMC pellets is only about 56% compared with that of pellets prepared from ordinary iron ore concentrate with relatively coarse particle size, which is
More
Iron Concentrate Particles - MDPI
2022.1.15 Iron ore concentrate is an output product from processed iron ores that have been milled (crush, grind, magnetic separation, flotation) to separate deleterious elements and produce a high-quality product. Sintering and pelletizing are economic and widely used agglomeration processes to prepare iron ore fines/iron concentrate for
More
Hydrogen reduction of low-grade banded iron ore
2022.9.1 The XRD analysis of magnetic concentrate reflects that the iron-bearing phases formed during the reduction are hematite, magnetite, and ferrite, and the phase fraction is shown in Fig. 8 (d). For experimental runs 1–3, there is a significant amount of unreacted hematite in the sample; hematite and magnetite are major phases and an ...
More
A novel process of reverse flotation-hydrogen reduction for
2023.2.15 TFe*—the iron content in ultra-pure magnetite concentrate, %; FeO*—the ferrous oxide content in ultra-pure magnetite concentrate, %. The controlling equations of interface chemical reaction and gas diffusion are expressed in equations (4), (5), where x, k and t separately represent the reduction degree, apparent rate constant and reaction time.
More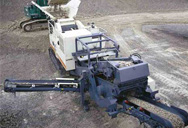
1,2,*, Yonghong Qin 1,2, Yuexin Han 1,2 and Yanjun Li 1,2
2022.4.18 Correspondence: [email protected]; Tel.: +86-24-8368-7120; Fax: +86-24-8368-8920. Abstract: In this study, a novel technology for the comprehensive utilization of low-grade iron ore is presented. For the iron ore with a Fe content of 24.91%, a pilot-scale study of pre-concentration, suspension magnetization roasting, grinding, and
More
Synthesis of magnetite powder from the mixture consisting
2018.6.15 The results show that for iron tailings with a mass of 12 g, a N 2 gas flow rate of 600 mL/min, and roasting for 5 min at 800 °C, iron concentrate with a 60.44% iron grade at an iron recovery of 76.04% could be obtained. X-ray diffraction analysis showed that the weak magnetic hematite was reduced to strong magnetic magnetite in the neutral ...
More
Influence of magnetite concentrate morphology on
2023.9.1 (1) [9]: (1) Oxidation degree, % = (1 − FeO T FeO 0) × 100 where FeO 0 and FeO T are the FeO content of initial magnetite iron ore concentrate and pellets indurated at various temperatures, respectively. The phase and structure of magnetite concentrate and BM and HPGR pellets were analyzed using an XRD method (AWXDM30-ASENWARC
More
Study of Temperature Profile in the Induration of Magnetite Iron Ore ...
2016.12.1 The iron ore pellets were prepared by using the raw materials of magnetite iron ore concentrate (−100 μm size), bentonite (−75 μm size) and limestone (−100 μm size). The detail chemical analysis of the raw materials is given in the Table 1. The major elements of magnetite ore were analysed by wet chemical analysis.
More
Optimization of Induration Cycle for Magnetite Concentrate
2020.10.26 In the magnetite iron ore pelletization process, oxidation of magnetite followed by sintering of the oxidized magnetite (hematite) is desirable. Optimum preheating time temperature and roasting time temperature is required to get the desired properties of the pellets with magnetite, hematite, and hematite–magnetite blend. In order to utilize
More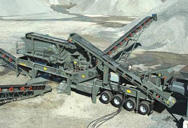
Flash Ironmaking SpringerLink
2022.4.20 The flash ironmaking technology is an innovative process that uses iron ore concentrate directly without further treatment. ... During the process at low temperature (above 843 K), the reduction proceeds from hematite Fe 2 O 3 via magnetite Fe 3 O 4 to wüstite FeO and finally to metallic iron Fe. Below 843 K, reduction occurs from magnetite ...
More
A new approach for recovering iron from iron ore tailings
2020.2.1 The chemical composition and iron phase composition of the iron concentrate are provided in Table 3, Table 4, respectively. The content of Fe was upgraded from 21.51% of the iron ore tailings to 58.67% of the iron concentrate, and the Fe in the iron concentrate was mainly present in the form of magnetite with a percentage of 97.87%.
More
The mechanism of suspension reduction on Fe enrichment
2022.7.1 Laboratory-scale SMR experiments were used to enrich the valuable iron minerals from the carbonate-containing iron ore. A laboratory-scale suspension roaster first roasted the carbonate-containing iron ore (30.0 g), further ground using a bar mill, and then a low-intensity magnetic separation via the magnetic tube, as shown in Fig. 1.All
More
Metals Free Full-Text Reduction Kinetics of Compact
2023.1.19 This reduction rate remains almost constant from about 20–80% reduction, decreasing to 0.3–1%/min for the completion of reduction from wüstite to metallic iron (FeO to Fe°). The reduction controlling mechanism was evaluated based on the calculated apparent activation energy and fitting the experimental data to one gas-solid reaction
More
Development of a Redox Microtitration Method for the
2022.1.31 The determination of the metallic iron content in the reduced iron ore concentrates is essential to evaluate the reduction efficiency in the process metallurgy field. In this study, a redox microtitration method was developed to determine the metallic iron content in the reduced micron-sized iron ore concentrate particles. The effects of the
More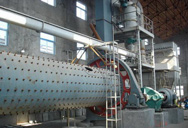
A Kinetic Study on the Reduction of Single Magnetite
2021.8.11 Bohn et al. carried out a study on the reduction kinetics of iron oxide in the gas mixtures of CO, CO 2, and H 2, and their results showed that the reduction from Fe 2 O 3 to FeO, including two steps from Fe 2 O 3 to Fe 3 O 4 and Fe 3 O 4 to FeO, was a first-order reaction in CO, and the reduction rate was controlled by intrinsic kinetics.
More
Improved iron recovery from low-grade iron ore by efficient
2022.8.1 During the reduction roasting stage, the hematite within iron ore powder was almost entirely transformed into magnetite at a reduction temperature of 520 °C using a gas combination of 45 % H 2 - 15 % CO- 40 % N 2, which significantly enhanced the magnetism of the particles. At this time, iron minerals could be effectively recovered by a ...
More
Pelletization of hematite and synthesized magnetite concentrate from
2021.10.1 The BHQ ore sample was obtained from one of the iron ore mines of Hospet located in the Karnataka state of India. The chemical analysis of the BHQ sample is given in Table 1.The sample was crushed to below 10 mm size, and a representative sample was drawn to generate hematite and magnetite pellet feed concentrates through the
More
Innovative utilization of refractory iron ore via suspension ...
2019.6.15 Next, the iron ore falls into the suspension-heating furnace under the action of gravity and is preheated again before being transported into the gas-solid cyclone separator by the hot-gas. The heated iron ore then enters the fluidized bed, and the reduction of hematite and siderite to magnetite occurs rapidly near the inlet of the CO
More