clinker cement wet dry process

ReviewA comprehensive review on Advanced Process
2023.1.1 Dry, wet, and semi-dry processes are the various types of raw milling operations used in the cement industries. Raw materials are dried using impact dryers, drum dryers, paddle-equipped rapid dryers, and air separators in the absence of water in the
More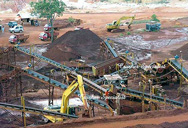
Review on energy conservation and emission reduction
2022.12.1 Energy consumption and emission reduction mainly depend on the kiln used in cement manufacturing. The dry process of cement manufacturing utilizes 3.40
More
Comparison of energy consumption and carbon emissions from clinker
2021.7.15 Developing a dry production process for recycled cement will reduce the CO 2 emissions to only 13% of the clinker. Abstract The in order to meet the targets set
More
Cement Manufacturing and Process Control SpringerLink
2019.8.27 Manufacturing process of Portland cement clinker is discussed, which is relevant to a Refractory technologist engaged in manufacturing or development of
More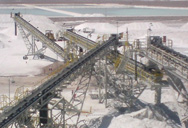
Cement Manufacturing—Technology, Practice, and
2021.11.17 There are four main types of processes used in cement manufacture: Dry Process, Semi-dry Process, Semi-wet Process, and the Wet process. In all these
More
A Review on Pyroprocessing Techniques for
2020.2.9 The major difference between wet and dry process is the mix preparation method before burning clinker in the kiln. The wet process involves the addition of water to the raw materials to form rawslurry
More
Wet process rotary cement kilns: modeling and simulation
2006.3.17 The description “dry” or “wet” process complies with the moisture content of the feed into the rotary kiln. While in a dry process the raw meal is first pre-dried and
More
Research Article Parametric Studies of Cement
2020.2.15 cement clinker. Regarding the type of pyroprocessing employed in RKS, the overall technology for cement produc-tion can be roughly divided into (i) the dry
More
(PDF) Cement Manufacturing - ResearchGate
2015.12.9 Figure (5): The Wet process of cement (Mahasenan, et.al 2008) 4.2 Semi-dry process It example to dr y process and uses a L epol kiln : in the lepol kiln the pellets are dried and
More
Wet process rotary cement kilns: Modeling and simulation
2006.5.1 Request PDF Wet process rotary cement kilns: Modeling and simulation The knowledge of wet process kilns design and operation in the cement industry has not
More
Process of Cement Manufacturing -A Brief into
2023.6.14 Cement manufacturing is an intricate process involving the extraction and grinding of raw materials, followed by blending and heating in a kiln to produce clinker. This clinker is then ground with gypsum to
More
Production of cement and its environmental impact
2023.1.1 The fuel consumption was high (1350–1500 kcal/kg clinker), but the electrical energy consumption (in kWh/t) was less compared to dry process. To save on fuel costs, the wet process is rarely used these days and the shift is toward dry process.
More
11.6 Portland Cement Manufacturing - U.S.
2021.11.10 In the wet process and long dry process, all of the pyroprocessing activity occurs in the rotary kiln. Depending on the process type, kilns have length-to-diameter ratios in the range of 15:1 to 40:1. While some wet process kilns may be as long as 210 m (700 ft), many wet process kilns and all dry process kilns are shorter.
More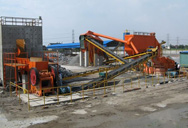
Cement Manufacturing—Technology, Practice, and
2021.11.17 The manufacturing of cement clinker was initially based on the “wet” process, but the “dry” process is today the state of the art. The “semi-wet” and “semi-dry” processes were intermediate. 4.1 The Dry Process. The raw meal is prepared by drying and grinding in ball mills or vertical roller mills.
More
Wet process rotary cement kilns: modeling and simulation
2006.3.17 At the present time some 80% of the global cement clinker production is obtained from dry kiln processes. However, there are still a several hundred wet process kilns in use (Eckert and Hand 2002; De Beus 1999).Modern dry process plants are a combination of a four-to-five-stage cyclone preheater and a pre-calcination followed by a
More
Wet Process Of Cement Manufacturing With Flow Chart
2 天之前 The process out clinker is cooled and ground to a fine powder with the addition of about 3 to 5% of gypsum. The material produced by this process is known as Portland cement. Cement manufacturing is done majorly by two methods known as wet process and dry process depending on their mixing is done with water or without water.
More
Wet Process vs. Dry Process Cement LUTON GROUP
5 天之前 Wet Process Cement. Dry Process Cement. Advantages. 1.High and stable quality, accurate ingredient ratio, durable service life after solidification. 2.Fluidity, nice homogeneity and perfect quality of clinker. 3.Lower energy consumption. 4. Suitable for mass production and more suitable for the use of cement in large and medium-sized
More
(PDF) Modern cement production with chalk - ResearchGate
2010.1.1 N. N. Zhanikulov. The main raw materials in the production of cement are carbonate and clay rocks, as well as some types of industrial and man-made waste. The bowels of Kazakhstan are rich in raw ...
More
Comparison of energy consumption and carbon emissions from clinker
2021.7.15 The shift from wet to dry process improved the energy efficiency from 26% to 58%. The use of alternative fuels and/biomass is now a standard in many countries, ... Regarding the Secil plant at Outão, the data is reported both in terms of the amount of clinker and cement produced (SECIL, 2011, 2014, 2016, 2018). In this plant, the
More
Dry Process of Cement Manufacturing Semi-dry Process
2022.4.8 The main difference between the dry process and wet process of cement manufacture is the way in which the raw materials are prepared before they are fed into the kiln.. In the dry process, the raw materials are ground and dried into a powder, which is then mixed and fed into the kiln. The raw materials are heated to a temperature that causes
More
11.6 Portland Cement Manufacturing - US EPA
1971.8.17 In the wet process and long dry process, all of the pyroprocessing activity occurs in the rotary kiln. Depending on the process type, kilns have length-to-diameter ratios in the range of 15:1 to 40:1. While some wet process kilns may be as long as 210 m (700 ft), many wet process kilns and all dry process kilns are shorter.
More
Review on energy conservation and emission reduction
2022.12.1 The dry process of cement manufacturing utilizes 3.40 GJ of specific energy per ton of clinker production, while the wet process utilizes 5.29 GJ/t. It has been reported that the specific energy consumption value for many countries is less than 2.95 GJ per ton of clinker, while the minimum value in India is 3.06 GJ ( Madlool et al., 2011 ,
More
(PDF) Cement Manufacturing - ResearchGate
2015.12.9 Figure (5): The Wet process of cement (Mahasenan, et.al 2008) 4.2 Semi-dry process It example to dr y process and uses a L epol kiln : in the lepol kiln the pellets are dried and
More
11.6 Portland Cement Manufacturing - U.S.
2022.3.22 In the wet process and long dry process, all of the pyroprocessing activity occurs in the rotary kiln. Depending on the process type, kilns have length-to-diameter ratios in the range of 15:1 to 40:1. While some wet process kilns may be as long as 210 m (700 ft), many wet process kilns and all dry process kilns are shorter.
More
Production Process CEMEX Philippines
Clinker is the intermediate product used in the manufacturing of cement. There are two primary processes used to manufacture clinker: the dry process and the wet process. Our plants use the dry process, which is more energy efficient. In the wet process, the raw materials are mixed with water to form slurry, which is fed into a kiln.
More
Emission Factor Documentation for AP-42 Portland
2021.6.25 population included 80 wet process kilns and 133 dry process kilns. Both the number of facilities and the industry capacity declined in 1990; two plants with a total annual clinker capacity of 492 x 10 3 megagrams
More
A critical review on energy use and savings in the cement industries ...
2011.5.1 In a wet process extra energy is needed to remove moisture contained in wet slurry. Industries around the world are moving towards dry manufacturing process as they consume less energy than a wet process. Dry process consumes about 13% less energy (electrical) than a wet process. Dry process found to consume about 28% less
More
Life cycle assessment of beneficial use of calcium carbide
2023.9.15 The main production processes of acetylene in China can be classified into dry-process and wet-process. The water content of CCS produced by the wet-process is high and needs to be dehydrated before it can be used for cement clinker production, whereas the water content of CCS produced by the dry-process is generally in the range
More
Cement - Extraction, Processing, Manufacturing Britannica
This grinding is done wet or dry, depending on the process in use, but for dry grinding the raw materials first may need to be dried in cylindrical, rotary dryers. ... The clinker may be immediately ground to cement or stored in stockpiles for later use. In the semidry process the raw materials, in the form of nodules containing 10 to 15 ...
More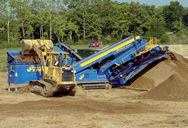
Fig. 12. Stages in cement production flow chart [43].
General Overview of Principles The wet and dry manufacturing processes are the two main ways of manufacturing cement [2]. The major difference between wet and dry process is the mix preparation ...
More
(PDF) A Review on Pyroprocessing Techniques for
2020.8.17 Figure 1 shows a process scheme that would apply to both the dry and the wet processes. Simplified cement production process [10]. Global clinker production per kiln type according to the GNR ...
More
Comparison of energy consumption and carbon emissions from clinker
2021.7.15 The main drawback of the recycled cement production process is the pretreatment stage related with washing and drying of waste materials. The carbon dioxide emissions from recycled cement production can be potentially reduced to only 13% of the emissions from clinker production, if these pretreatment stages are avoided by
More
Clinker Production - Clinker Manufacturing Cement
Cement kiln is the main equipment for clinker sintering. From structure, it can be divided into rotary cement kiln and shaft kiln, while, from the working principle, it can be divided into the dry method and wet method kiln. AGICO offers different types of cement kilns from 10-5000t/d with steady running, high efficiency and large output.
More
I03 cement June 2010 GS-gct - IEA-ETSAP
2022.4.11 that of dry powders. The wet process also enables an easier control of the chemical composition of the raw mix. However, the wet process is more energy intensive and Fig. 1 - Simplified cement production process[5] Tab. 1 – Cement EU Standard and Composition [5] Types of cement Clinker Other Constituents CEM I Portland 95-100 CEM II
More
What is the manufacturing process of Portland Cement?
The materials, without the gypsum, are proportioned to produce a mixture with the desired chemical composition and then ground and blended by one of two processes – dry process or wet process. The materials are then fed through a kiln at 2,600º F to produce grayish-black pellets known as clinker.
More
Cement Production - an overview ScienceDirect Topics
The production of cement is either through the wet or dry process with the dry process as the preferred option because of the lower energy intensity. Cement production accounts for about 5% of total anthropogenic emissions (IFC, 2017). Cement-based structures constitute the largest surface area of all man-made structures (Odigure, 2009).
More
Cement kiln dust - ScienceDirect
2022.1.1 Dusts are collected from electrostatic precipitators during the production of the clinker. Cement kiln dust is fine particles similar in appearance to Portland cement. If the clinker production takes place in a wet process, the dust is collected in the form of a suspension, if the clinker production is dry, the dust is collected in a dry form.
More
11.6 Portland Cement Manufacturing - U.S.
2022.3.22 In the wet process and long dry process, all of the pyroprocessing activity occurs in the rotary kiln. Depending on the process type, kilns have length-to-diameter ratios in the range of 15:1 to 40:1. While some wet process kilns may be as long as 210 m (700 ft), many wet process kilns and all dry process kilns are shorter.
More
Cement Production Process Cement Manufacturing Process AGICO CEMENT
2020.8.25 There are three steps of the high-temperature system: Drying or preheating, calcining, and sintering. The calcining is the core part of the clinker production; the raw meal is weighed and sent into preheater and cement kiln to process clinker. Grate cooler helps to cooler clinker, the cooled clinker is sent to the cement silo for storage.
More
Study and Review of Ordinary Portland Cement
2022.2.2 grinding is done wet or dry, depending on the process in use, but for dry grinding the raw materials first may need to be dried in cylindrical, rotary dryers. ... The clinker may be immediately ground to cement or stored in stockpiles for later use. In the semidry process the raw materials, in the form of Modules containing 10 to 15 ...
More