Ball Mill Limestone Particle Size

Influences of ball-milled limestone particle sizes and shapes
2020.9.20 Three distinct filler particle fractions were produced by a planetary high-energy ball mill from limestone aggregates (2.36–4.75 mm). Their particle sizes and shapes were studied by binary image processing and related to milling time and aperture size.
More
Particle size distribution and structural changes in limestone
2014.1.10 The dry grinding of limestone in a planetary ball mill was investigated as a function of the diameter of the grinding balls and the revolution speed of the mill. The
More
Energy-Model and Life Cycle-Model for Grinding
2022.4.17 The median particle size of stirred ball grinding is X 50 = 17.62 μm for the feed limestone material. After wet grinding of 20 min in the laboratory stirred ball mill, the median particle size of ground limestone is
More
Particle size distribution and structural changes in limestone
2013.1.1 The experimental mill used was a laboratory size of 209 mm diameter, 175 mm length, providing a total mill volume of 6001 cm3, with a total mass of 5.6 kg of steel
More
Influences of ball-milled limestone particle sizes and shapes
2020.9.1 The effect of milling time on particle size, morphology, purity, and microstructure of quartz was examined. Results indicate that particle size reduced by >96%.
More
The design and optimization process of ball mill to reduce particle ...
2020.11.16 Particle size plays an important role in the designs of calcium carbonate-based material. Small particle size in the order of micrometer of event nanometer size is
More
Discussion and application of ball mill in preparation of particle size ...
2023.5.1 The conditions for separating particles of fine grained sedimentary rocks by ball mill are determined as follows: sample mass is 0.14 g ~ 0.20 g, ball mill frequency is
More
Effects of Ball Milling Processes on the Microstructure and
2018.6.22 It was obtained that melting onset temperature of products gradually decreased from 333.56 °C to 321.42 °C as a consequence of particle size reduction,
More
Selected Advances in Modelling of Size Reduction in Ball Mills
2023.9.22 The first task is establishing the optimum values of various mill design and operating variables, such as the mill speed, ball load, particle load, and ball diameter
More
Optimization of Ball Mill Grinding of a Limestone-Type
2023.4.13 The effect of ball size and interstitial filling on the performance of dry ball mill grinding was investigated for a limestone-type brecciated uranium ore. The optimum
More
Limestone Milling Process - Gravel Mill
The ball mill is intended to grind limestone, which is a rather soft material, to the desired fineness. The grinding and crushing of the limestone particles is done by the grinding medium, which are typically steel balls, inside the
More
Ball Mill - an overview ScienceDirect Topics
where d b.max is the maximum size of feed (mm); σ is compression strength (MPa); E is modulus of elasticity (MPa); ρb is density of material of balls (kg/m 3); D is inner diameter of the mill body (m).. Generally, a maximum allowed ball size is situated in the range from D /18 to D/24.. The degree of filling the mill with balls also influences productivity of the mill
More
Influences of ball-milled limestone particle sizes and shapes
2020.9.20 2.1.2. Filler. This study used limestone aggregates from a local quarry with a nominal size range of about 2.36–4.75 mm. The aggregates were ground at room temperature by a planetary high-energy ball mill equipped with a 500 ml ball mill tank and 6 mm- and 10 mm-diameter zirconium oxide balls [21].In order to improve the efficiency of
More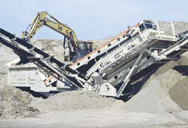
A cement Vertical Roller Mill modeling based on the
2022.10.1 Matrix model's results model provides a more robust prediction based on the number of 2-times clinker breakage in VRMs (R = 0.9916, MSE = 5.3526, accuracy = 94.6474). Also shown by the results of the matrix modeling, the S increased with decreasing the particle size. In contrast, the population balance model increased with increased
More
Technical Process of Wet Ball Mill Produced by HXJQ ...
2013.10.16 Technical Process of Wet Ball Mill Produced by HXJQ. General Wet Ball Mill feed size of 80% particles of less than 12mm.Regulation of entrance feed mill.General to reduce electricity consumption, mill should be routinely maintained in rated operation conditions, but sometimes as a result of a variety of reasons, the steel ball added is not ...
More
Ball mill characteristics and test conditions Mill Diameter, D
The use of either 25.4 mm balls or a mixed load of balls with varying sizes results in 31 and 24% decrease in energy requirements, compared to the use of balls with small size (12.7 mm). View
More
A study of the intergrinding of clinker and limestone
1999.7.1 Four clinkerllimestone mixtures, containing 10, 20, 30 and 40% limestone respectively, were ground to 4 different degrees of fineness, and a sedimentation method was used in order to collect samples of different particle size. In each size fraction the limestone content was determined and finally the particle size distribution of clinker and ...
More
Mechanistic modeling and simulation of a batch vertical stirred mill ...
2020.9.1 Snapshot of DEM simulations of vertical stirred mill charged with 86.8 kg of 20 mm grinding media and screw shaft rotating at 3 m/s (a), 2.5 m/s (b) and 2.0 m/s (c). Grinding media are colored by their velocity. The collision energy spectra of the mill can be observed in Fig. 5, showing the normal, tangential and the total energy dissipated ...
More
C110 Standard Test Methods for Physical Testing of
2017.1.11 Dry Brightness of Pulverized Limestone. 12. Limestone Grindability Determination by the Laboratory Ball Mill Method. 13. Settling Rate of Hydrated Lime. 14. Particle Size Analysis Residue and Sieve Analysis. 15. Sieve Analysis of Dry Limestone, Quicklime, and Hydrated Lime. 16
More
A Review of Alternative Procedures to the Bond Ball Mill
2021.7.12 It can be performed in any laboratory ball mill, but it requires a reference sample ore for which w i is known. In the Berry and Bruce procedure, 2 kg weight samples of the reference and unknown ores with a particle size under 1.651 mm are wet ground in a laboratory ball mill that is 305 mm in diameter, using active power monitoring.
More
Jet mill grinding of portland cement, limestone, and fly
Request PDF On Nov 1, 2013, Hongfang Sun and others published Jet mill grinding of portland cement, limestone, and fly ash: Impact on particle size, hydration rate, and strength Find, read and ...
More
(PDF) Grinding in Ball Mills: Modeling and Process
2012.6.1 Besides particle size reduction, ball mills are also widely used for mixing, blending and dispersing, amorphisation of materials and mechanical alloying [1, 49, 51].
More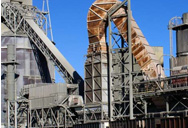
Influence of raw material particle size on quality of pellets
2013.7.18 Iron ore fines of −10 mm size and limestone are ground together in a ball mill to get sufficient fineness for the balling process. However, as limestone is harder than iron ore fines the + 100 mesh size limestone particles is higher than required and not all the limestone is fully consumed in the reaction for melt formation.
More
AMIT 135: Lesson 7 Ball Mills Circuits – Mining Mill
Ball Size as Initial Charge. Commercial ball sizes 10 – 150 mm; Number, size and mass of each ball size depends on mill load and whether or not the media is being added as the initial charge. For the initial chargin of a mill, Coghill and DeVaney (1937) defined the ball size as a function of the top size of the feed, i.e., d↓V = 0.40 ...
More
Effect of Slurry Concentration on the Ceramic Ball Grinding ...
2022.12.6 Ceramic grinding, which in this paper is defined as a method of using ceramic materials as grinding media, is favored by many processing plants as an emerging high-efficiency and energy-saving grinding method. This paper investigates the effect of slurry mass concentration on the grinding characteristics of magnetite by taking the feed
More
Wet and dry grinding of coal in a laboratory-scale ball mill: Particle ...
2020.1.1 Thus, it is important to control the particle size or particle-size distribution (PSD) in a ground product. The efficiency of size reduction is influenced by a number of variables including the mill speed, ball size, filling rate, feed size distribution, pulp density, coal rank, the mode of grinding (wet or dry), material hardness, and ...
More
Comparative comminution efficiencies of rotary, stirred and
2021.7.15 Here we explore the energy performances of ball mills for extensive particle size reduction on two lignocellulosic biomasses of contrasting types (pine bark, which is a fragile layered material, and wheat straw, which is a tenacious fibrous material). Target particle size was set at 20 μm, to allow direct use of the feedstock for energy in ...
More
Multifractal characterization of gangue particle size
2022.11.1 To explore the PSD structural characteristics of gangue under ball milling time, firstly, the gangue samples from each lithology were manually screened and evenly mixed to create three types of gangue samples with the same initial particle size distribution presented in Fig. 3 (a).Then 5 kg gangue samples were weighed and filled into the ball
More
Jet mill grinding of portland cement, limestone, and fly ash:
2013.11.1 The first system is a blend of OPC and 15% limestone, and the second system is a blend of OPC and 40% fly ash. It was observed that when jet mill grinding is used, the average particle size of the powders is decreased to approximately 4 μm or less with a narrower particle size distribution than that achieved using ball milling.
More
Optimization of Ball Mill Grinding of a Limestone-Type
2023.4.13 The effect of ball size and interstitial filling on the performance of dry ball mill grinding was investigated for a limestone-type brecciated uranium ore. The optimum grinding was obtained with the combination of different balls (12.7–37.5 mm) and interstitial filling of 50% (20% ball filling ratio at fixed material filling ratio = 4%). The net power
More
Prediction of ball milling performance by a convolutional
2022.5.1 1. Introduction. Ball milling is a critical process to reduce product size into a desired size range, which has been widely used in industries such as minerals processing, cement manufacturing, pharmaceutical industries and powder metallurgy [1, 2].The milling process is affected by many parameters, including ground particles, mill speed [3], milling
More
What Should We Note When Operating the Ball
2018.9.17 Generally, too large limestone particle size will cause the extra burden to the ball mill, and some super-large limestone particles are not easy to be crushed by the steel ball, which not only ...
More
Grindability of binary ore blends in ball mills - ScienceDirect
2013.2.1 Upon conclusion of each Bond ball mill grindability test, products have been analyzed in respect to size distribution and composition. Fig. 2 summarizes results from these analyzes for each individual component in a blend of basalt and limestone #1. It suggests that the product size distribution of the hard component (basalt) did not vary if it ...
More
Estimation of the Specific Energy Requirement for Size Reduction
2016.11.8 where \(y_{p}\) is the 80% passing size of the mill product, \(y_{f}\) is the 80% passing size of the mill feed, C is a mill-material constant, and α is the exponent of particle size (its significance discussed in detail later). It has been shown [] that the value of the exponent α varies strongly with the material type, generally in the range of 0–2.
More
The influence of suspension properties on ultra-fine grinding
1999.11.1 The mills traditionally used for wet ultra-fine grinding are high-speed stirred ball mills. The aim of the research was to investigate the influence of the solid (limestone) concentration and of the concentration of sodium polyacrylate on the apparent viscosity and the grinding efficiency. With increasing solid concentration the energy ...
More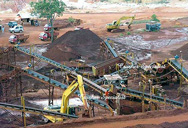
(PDF) EFFECT OF PARTICLE SIZE DISTRIBUTION ON GRINDING
2012.9.24 It is well known that in rod and ball mills the size distribution of the particulate material varies along the mill [17,[29][30][31] and the breakage rate of particles varies with the particle ...
More
Optimization of Ball Mill Grinding of a Limestone-Type
2023.4.13 The effect of ball size and interstitial filling on the performance of dry ball mill grinding was investigated for a limestone-type brecciated uranium ore. The optimum grinding was obtained with ...
More
A Review of the Grinding Media in Ball Mills for Mineral
2023.10.27 The ball mill is a rotating cylindrical vessel with grinding media inside, which is responsible for breaking the ore particles. Grinding media play an important role in the comminution of mineral ores in these mills. This work reviews the application of balls in mineral processing as a function of the materials used to manufacture them and the
More
Ball mill characteristics and test conditions Download Table
This paper presents the kinetics study of dry ball milling of calcite and barite minerals. The experimental mill used was a laboratory size of 209 mm diameter, 175 mm length, providing a total ...
More