roller mill grinding méthode

Roller Mill - Springer
2023.7.4 Roller mill is a type of grinding equipment for crushing materials by pressure between two or more rolling surfaces or between rolling grinding bodies (balls, rollers) and a track (plane, ring, and table).
More
Grinding process within vertical roller mills: experiment and ...
2009.1.1 Based on screening analysis, laser size analysis, grindability and rigidity tests of samples collected on line from a cement and a power plant, a simulation of the
More
(PDF) Analysis and Optimization of Grinding Performance of
2022.1.23 PDF This work concentrates on the energy consumption and grinding energy efficiency of a laboratory vertical roller mill (VRM) under various operating...
More
Roller mills: Precisely reducing particle size with greater
2020.11.11 This article introduces roller mills and explains how they efficiently grind friable materials to a uniform final particle size while using relatively little energy
More
A study of operating parameters of a roller mill with a new
2019.2.21 The paper analyzes the interrelation of: motion, particle size of ground rice grains, displacement, and grinding in a roller–plate mill. The purpose of the study was to
More
Roller Mill Based on Experimental Method - mdpi-res
2022.1.23 mill, coal mill, Clinker Mill and cement mill, and the vertical mill occupies a large energy consumption unit. Therefore, it is necessary to optimize the multi-objective
More
Selected Aspects of Modelling and Design Calculations
2021.3.1 For calculation purposes it has been assumed that the diameters of the rollers d in the mill were within the scope from 270 to 320 mm at their width s = 100 mm
More
PROCESS CONTROL FOR CEMENT GRINDING IN
2017.10.27 Roller Mill (VRM) reduces the power consumption for cement grinding approximately 30-40% associated with other grinding mills. The process variables in
More
Modeling and Industrial Development of Grinding Processes in Roller ...
2022.9.12 A model of the capture of material by corrugated rollers in a crusher is described. A formula is proposed for the wrapper dimensions and the angular distance
More
(PDF) Analysis and Optimization of Grinding Performance of
2022.1.23 Productivity increase of the vertical roller mill for cement grinding. In Proceedings of the IEEE Cement. Industry T echnical Conference, Hershey, P A, USA, 20–24 April 1997. 10.
More
From Quern to Computer: The history of flour milling - Mills
2016.9.6 W. Vernon Son’s New Flour Mills at Birkenhead, 1899 (Bennett and Elton 1900, opposite p.309) (MWAT-024) The roller mill at the turn of the century is perhaps epitomised by Vernon Sons’ mill at Birkenhead, Liverpool which opened in 1899. Built on the latest Simon system, the mill had two separate milling plants, one with nine 60 inch
More
eFeedLink - Feed milling technologies, Part II: Basic roller mill
Mills used to flake grains or other products may be called flaking mills or flakers. Roller mills used to grind in a feed mill are commonly referred to as a roller mill or roller mill grinder. Double pair (two pair high) roller mills may be utilized in feed milling operations when two distinctly different grains are processed through one mill.
More
G1613 Roller k - Exercice complet sur le target costing
Chapitre 4-Méthode d ordonnancement, MPM. Introduction aux techniques de Gestion 100% (16) 8. Chapitre 1 - L entreprise et son organisation. ... Le Roller en ligne s'adresse à une cible clairement identifiée, qu'on peut décomposer en 3 catégories. L'ensemble de la cible est plutôt jeune puisque la moyenne d'âge des utilisateurs de Roller ...
More
Energy-Efficient Technologies in Cement Grinding IntechOpen
2016.10.5 The energy consumption of the total grinding plant can be reduced by 20–30 % for cement clinker and 30–40 % for other raw materials. The overall grinding circuit efficiency and stability are improved. The maintenance cost of the ball mill is reduced as the lifetime of grinding media and partition grates is extended. 2.5.
More
Influence of quartz particles on wear in vertical roller mills.
2010.4.1 Semantic Scholar extracted view of "Influence of quartz particles on wear in vertical roller mills. Part I: Quartz concentration" by L. Jensen et al. Skip to search form Skip to ... study is directed to the temperature and residual stress fields in the hardfacing remanufacturing for a large-scale grinding roller with damage. For this purpose, a ...
More
Size reduction in feed technology and methods for
2020.3.1 Different grinding methods, including the use of roller mills, hammer mills, multicracker and multi-stage grinding were reviewed. Roller milling tends to produce a more uniform particle size distribution (PSD) and consumes less energy, whilst hammer mills have a greater grinding capacity and a higher reduction ratio compared to roller mill.
More
三辊研磨机 研磨与分散 布勒集团 - BUHLERGROUP
我们的三辊研磨机具有可靠、高产量以及对污染物和温度敏感物料柔和分散等突出特性,帮助您实现高质量研磨和分散。. 我们的研磨机提供各种磨辊材料和方案,满足清洁生产到国际标准等各种应用要求。. +. 产品范围.
More
A study of operating parameters of a roller mill with a new
2019.2.21 The paper analyzes the interrelation of: motion, particle size of ground rice grains, displacement, and grinding in a roller–plate mill. The purpose of the study was to analyze and evaluate ...
More
The working principle of vertical roller mill - ITPUB博客
2015.3.9 From the working principle known the vertical roller mill: One, the grinding roller and the grinding disc must remain on the material layer grinding enough pressure, so that the material is rolled and crushing. The grinding pressure is roller pressure, it and the material grindability, moisture, wind speed, grinding and production requirements ...
More
Modeling and Industrial Development of Grinding Processes in Roller ...
2022.9.12 where R w is the wrapper’s working radius; b is the distance between the rollers (the width of the output slot); r p is the conventional radius of the piece; and γ fr is the frictional angle of the material at the wrapper surface. We know that γ fr = tan μ, where μ is the frictional coefficient of the material being crushed at the wrapper.. In the present
More
Comparison of the overall circuit performance in the cement
2011.2.1 1. Introduction. Tube mills having multi-chambers are traditionally used for cement grinding either in open or closed circuit operations. In the first chamber, larger balls (100–60 mm) are used for coarse grinding while the smaller balls (40–15 mm) are used for fine grinding.The chambers are separated by an intermediate diaphragm which allows
More
The Evolution of Milling Process SpringerLink
2021.4.20 It is supposed that the mills consisting of two grindstones appeared in ancient Egypt but the archaeological finds from 1000 BC at the Boden Lake in modern Switzerland and around Dresden and Leipzig in modern Germany also reported similar grinding stones [7, 12].Very important feature of this grinding instrument is a shift from
More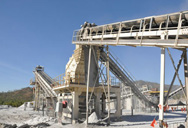
Key Industry Program - Castolin Eutectic
2019.10.30 rily. Final results provide a higher grinding capacity as well as a reduction of mill energy consumption. The avoidance of having to weld thick wear facing deposits also implies less risk for clients during ope-rations as such coatings may spall. For cement grinding, significantly refined levels are needed compared to raw material grinding
More
WO2015015507A1 - A grinding roller for vertical roller mill
2013.9.27 The Present invention provides a grinding roll for vertical roller mill comprising of roll body (2) having inner periphery (4) and outer periphery (3) and at least one insert (5) being placed inside the roll body (2). The insert (5) is placed inside the roll body (2) such that the insert (5) is near to the inner periphery (4) of roll body and away from the
More
Milling and flour quality - ScienceDirect
2012.1.1 Modern flour milling has three defining features (Storck and Teague, 1952, pp. 241–2 241 242): the use of a longer gradual reduction process, full automation, and the complete displacement of millstones by steel roller mills.The gradual reduction process, where repeated milling and sifting operations are performed using a sequence of
More
HRM型立式磨系列(PFRM系列)说明书(全)鹏飞产品 ...
HRM vertical roller mill is a sort of drying and grinding equipment with the characteristics of high efficient, economical energy and environmental protection; it is the equipment made by Jiangsu Pengfei Group Co., Ltd. intimately cooperated with the large institute
More
Comminution SpringerLink
2015.2.2 As with any material, rock particles only break when the applied tensile stress exceeds the tensile strength of the rock. However, in terms of comminution, the main interest is to derive reliable ways of assessing how a particular material breaks in a comminution device such as a crusher or a mill [].In general, the breakage of rock
More
Energy-Efficient Comminution: Best Practices and Future
2017.11.2 The most widely used grinding technologies include SAG, rod, and ball mills. Tower mills were introduced to the metal mining industry in the 1970s and the industry applied them, mostly, to applications with target grinds below 20 μm. High-speed stirred mills have been used for grinding clays, calcium carbonates and other powders for some time.
More
Selected Aspects of Modelling and Design Calculations
2021.3.1 For calculation purposes it has been assumed that the diameters of the rollers d in the mill were within the scope from 270 to 320 mm at their width s = 100 mm (Table 1). The assumed system of values d and s meet the guidelines concerning roller mills’ design, according to which s/d = 0.27–0.32.
More
quadropol® - thyssenkrupp Polysius
The quadropol® concept for coal or pet coke grinding, with adapted table speed and high efficiency separator sepol®, ensures a safety mill operation and serves reliable the kiln burning process. Mombasa Cement Ltd.
More
Premium solutions for the cement industry - FLSmidth
SAG Mill; Roller presses Roller presses. High pressure grinding roll (HPGR) HPGR Pro High Pressure Grinding Roll; Stirred mills Stirred mills. FLSmidth® Tower Mill (FTM) ... PERI™ AutoCharge Mill Grinding Ball Charging System. Back. PERI™ Online Slurry Analysis System. Back. Transfer Point Alignment Automation. Back. Conveyor Volume Flow ...
More
外文翻译(中英文)立式辊磨机_百度文库
Proven commercially,the OK mill is the premier roller mill for finish grinding of portlandcement,slag and blended cemtrents. With a 30%—45% reduction in the energy requirements for cement grinding and 40%—50%for slag as com—pared with traditionalball mill operations, the OK mill can contribute significantly to your profitability and
More
An investigation of performance characteristics and
2020.8.12 Altun et al [15] explored the influence of the parameter settings of a vertical roller mill on grinding performance and demonstrated the influence of grinding pressure values on the size and mass ...
More
Q. Fang, E. Haque, C. K. Spillman, P. V. Reddy. J. L. Steele
2009.1.15 roll power, slow roll power and net power significantly. Roll gap had a significant effect on roller mill grinding. Additional milling tests were conducted by randomly selecting independent variables and covariates to verify the robustness and validity of the prediction models. Keywords. Wheat, Wheat hardness, Grinding, Roller mill, Energy.
More
A data-driven decision-making framework for online control
2020.5.1 Introduction. Vertical roller mill (VRM) is a type of heavy-duty and energy-intensive grinding equipment for many industries, such as cement, steel and chemical industries. It is used to grind slag, nonmetallic ore and other block and granular raw materials into required powder materials. The fine powders can be used as raw materials
More
Cement grinding Vertical roller mills VS ball mills
For a ball mill grinding OPC to a fineness of 3200 to 3600 cm2/g (Blaine) the cost of wear parts (ball, liners and mill internals) is typically 0.15-0.20 EUR per ton of cement. For an OK mill grinding a similar product, the cost of wear parts depends on the maintenance procedures, i.e. whether hardfacing is applied.
More
Industrial mineral powder production in China - ScienceDirect
2007.12.1 During the past decade, due to the development of paper-making industry, the annual output of GCC has been increased by at least 10%, causing the rapid development of the corresponding technology for grinding calcium carbonate into ultra-fine products, in particular, large stirred bead mills for wet ultra-fine grinding with mill volume
More
DRIVE SELECTION FOR LARGE LOESCHE VERTICAL
2017.8.12 The drive of a vertical roller mill – essentially the mill gearbox – has to fulfill two tasks: The first is to reduce the speed of the electric motor to the selected mill speed and to transmit the torque created by the motor. Secondly, the gearbox has to transmit the grinding forces generated by the grinding rollers, from the mill table ...
More
US6193176B1 - Cement clinker grinding method using vertical roller mill ...
US6193176B1 US09/020,417 US2041798A US6193176B1 US 6193176 B1 US6193176 B1 US 6193176B1 US 2041798 A US2041798 A US 2041798A US 6193176 B1 US6193176 B1 US 6193176B1 Authority US U
More