mill occasion mineral grinding

A Review of the Grinding Media in Ball Mills for Mineral
2023.10.27 Grinding media play an important role in the comminution of mineral ores in these mills. This work reviews the application of balls in mineral processing as a
More
A Review of the Grinding Media in Ball Mills for Mineral
2023.10.27 pharmaceutical industries normally use dry grinding whereas the mineral processing in-dustry mostly resorts to wet-milling. In mineral processing, grinding, which
More
A process mineralogy approach to study the efficiency of
2020.12.3 Crushing and grinding processes are typically used by crushers and mills to liberate minerals, which are energy-intensive processes (especially fine grinding by
More
The Effect of Grinding Media on Mineral Breakage
2021.10.18 Abstract. The breakage and liberation of minerals are the key to fluidized mining for minerals. In the ball milling process, steel balls function as not only a grinding action implementer but also energy carrier
More
Mine operating costs and the potential impacts of energy and grinding ...
2014.2.1 The study looks at patterns in mining type, mill processing type, mineral type, and the differences between costs expressed in feasibility studies vs. operating
More
Modeling of Bauxite Ore Wet Milling for the Improvement of
2021.9.5 This study aimed to model bauxite grinding and assess the optimum material filling volume in a laboratory ball mill in order to improve mill and overall process
More
Copper ore grinding in a mobile vertical roller mill pilot plant
2015.3.10 Vertical roller mills (VRM) have been used extensively for comminuting both cement raw materials and minerals like limestone, clinker, phosphate, manganese,
More
Ultra-fine grinding and mechanical activation of mine waste
2017.1.10 Forsterite makes up the majority of the content and contributes to CO 2 2 kWh/t specific milling energy input after one hour direct aqueous carbonation. For the
More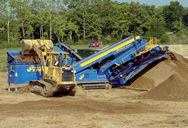
Minerals Free Full-Text Correction: Liao et al. A
6 天之前 Correction: Liao et al. A Comparison of the Fine-Grinding Performance between Cylpebs and Ceramic Balls in the Wet Tumbling Mill. Minerals 2022, 12, 1007 . by Ningning Liao. Ningning Liao. ... A
More
A Review of the Grinding Media in Ball Mills for Mineral
2023.10.27 The ball mill is a rotating cylindrical vessel with grinding media inside, which is responsible for breaking the ore particles. Grinding media play an important role in the comminution of mineral ores in these mills. This work reviews the application of balls in mineral processing as a function of the materials used to manufacture them and the
More
(PDF) LEARNING FROM OTHER INDUSTRIES; WHY THE VRM
2019.4.16 Research of iron ore grinding in a vertical-roller-mill, Minerals Engineering 73 (2015), 109–115 . Roy, G.R. (2002). ... These mills combine crushing, grinding, classification and drying ...
More
Grinding Mills Mineral Processing Equipment CITIC HIC
2023.12.21 To date, CITIC HIC has cumulatively produced and delivered over 1,550 mineral grinding mills, with a total installed power of 3,900MW. Our large-size grinding mills hold a market share of 85% in the domestic mining market, and have been exported to more than 50 countries and regions. This means that we are a world's leading manufacturer
More
Minerals Free Full-Text Study on Quantitative Separation
2023.4.6 Based on batch grinding method and normalization idea, a conical ball mill is used and a quantitative separation method of grinding characteristics of multi-component complex ore is proposed. The results show that the feed sizes of polymetallic complex ore have an obvious influence on the particle size distribution of intermediate grinding
More
Minerals Free Full-Text Performance Comparison of the
2023.1.31 Varied types/geometries of stirred mills have been produced by different manufacturers, and the comparison task has been accomplished for some of the technologies, i.e., Tower mill vs IsaMill. However, the main drawbacks of these comparisons were the uncommon characteristics of the milling environment, such as media size. In
More
Minerals Free Full-Text Grinding Media Motion and
2021.2.11 Product fineness during grinding in stirred media mills is mainly influenced by the specific energy input, the stress energy transferred by the colliding grinding media and the stress frequency. The stress energy from grinding media collisions is heterogeneously distributed in stirred media mills. Herein, in order to characterize the
More
Minerals Special Issue : Grinding Modeling and Energy
The results show that grinding time is a significant factor affecting the particle size composition. The suitable grinding concentration of Tongkeng ore and Gaofeng ore is 70% and 75%, respectively. The effect of mill filling ratio on Gaofeng ore is not obvious. The rotational rate has little effect on the grinding technical efficiency.
More
Minerals Free Full-Text Enhanced Flotation of Dolomite
2023.11.13 In the field of mineral processing, the successful flotation of target minerals requires sufficient liberation through grinding. The aim of this paper is to compare and evaluate the performance of ball versus short cylindrical media for comminution of dolomite by point and line contact, respectively. The results of the grinding experiments
More
Effect of particle shape and roughness of talc mineral
2004.2.16 A laboratory ball mill having 200 by 184 mm dimension with 5.475 kg of stainless steel balls of 30 and 26 mm in size were used. Feed sizes of the minerals were −850+600 μm with a. Results and discussion. Table 2 shows the values determined by SEM technique for the shape properties of talc mineral ground in different mills.
More
Metals Free Full-Text Variability Study of Bond Work Index
2021.6.17 It is a well-known fact that the value of the Bond work index (wi) for a given ore varies along with the grinding size. In this study, a variability bysis is carried out with the Bond standard grindability tests on different critical metal ores (W, Ta), ranging from coarse grinding (rod mills) to fine grinding (ball mills). The relationship between wi and grinding
More
Impact of grinding aids and process parameters on dry stirred media ...
2018.7.15 The dry fine grinding experiments were carried out in a self-constructed batch-wise operated vertical stirred media mill shown in Fig. 1. The agitator is driven by a Dispermat AE-06 by VMA-Getzmann, Germany. The mill consists of a 1.6 L stainless steel grinding chamber (2). The chamber was designed with rounded edges to ensure a
More
A process mineralogy approach to study the efficiency of
2020.12.3 As can be seen in Fig. 6B, the minerals present in the product of open-circuit mill, in the order of abundance, include molybdenite, which is mostly free and has become fine after grinding in mill ...
More
The 11 Best Salts of 2024 - The Spruce Eats
2023.6.14 The five main salt categories are table salt, kosher salt, sea salt, curing and brining salt, and specialty and seasoned salts, which can be either salt from a special location, such as Himalayan pink salt or Hawaiian black salt, or regular salt with a flavor added, such as garlic salt or celery salt.
More
A Review of Alternative Procedures to the Bond Ball Mill
2021.7.12 Over the years, alternative procedures to the Bond grindability test have been proposed aiming to avoid the need for the standard mill or to reduce and simplify the grinding procedure. Some of them use the standard mill, while others are based on a non-standard mill or computation techniques. Therefore, papers targeting to propose a better
More
Minerals Free Full-Text Effect of Grinding Media Size on ...
2021.12.27 The aim of this study is to evaluate the effect that the size of grinding media exerts on ferronickel slag milling efficiency and energy savings. A series of tests were performed in a laboratory ball mill using (i) three loads of single size media, i.e., 40, 25.4, and 12.7 mm and (ii) a mixed load of balls with varying sizes. In order to simulate the
More
Minerals Free Full-Text Effect of Intensive Abrasion
2023.5.23 Industrial application results show that after the abrasion of the secondary ball mill for grinding magnetite was enhanced, the circulating load of the grinding-classification system dropped by 29.90% and the specific energy of the secondary ball mill decreased by 39.14%. ... Fan, G.; Gao, M. The Effect of Grinding Media on Mineral
More
Modeling of Bauxite Ore Wet Milling for the Improvement of
2021.9.5 Size reduction is a necessary operation in mineral processing plants and provides the desired size for separation operations and the liberation of the valuable minerals present in ores. Estimations on energy consumption indicate that milling consumes more than 50 % of the total energy used in mining operations. Despite the fact that ball
More
MINERAL PROCESSING - MILLING - Internet Archive
2014.2.21 Rod mills are used for grinding hard minerals. This type of mill is usually used as the first stage of a milling process to provide a reduced size feedstock for a further milling process. Coke Products for the glass industry Cement clinker (needs to be dry) Table 5: Material Suitability for Rod Mills
More
MINERAL PROCESSING - MILLING - United Diversity
2020.12.4 Introduction. Milling, sometimes also known as fine grinding, pulverising or comminution, is the process of reducing materials to a powder of fine or very fine size. It is distinct from crushing or granulation, which involves size reduction to a rock, pebble or grain size. Milling is used to produce a variety of materials which either have end ...
More
Minerals Free Full-Text Ceramic Grinding Kinetics of Fine
2023.9.10 Aiming to reveal the kinetic characteristics of ceramic ball grinding of fine magnetite comprehensively, two types of ceramic balls ground with the same filling rate and total weight as steel balls were researched. The results show that the breakage rate of ceramic ball grinding is only half of that of steel ball grinding with the same media filling
More
Minerals - Weir Group
2022.11.4 Weir Minerals is committed to delivering market-leading mill liners combining state-of-the-art technology and innovative design with unparalleled service to all our customers across the world. The grinding circuit is the most abrasive application that process equipment endures. At Weir Minerals, we’ve invested in formulating
More
Minerals Free Full-Text Research on Grinding
2022.10.13 Grinding plays an important role in mining, construction, metallurgy, chemical, coal and other basic industries. In terms of beneficiation, grinding is the most energy consuming operation. So,
More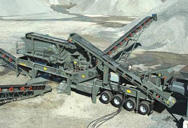
Machine Learning and Deep Learning Methods in Mining
2020.6.16 Semi-autogenous grinding mills play a critical role in the processing stage of many mining operations. They are also one of the most intensive energy consumers of the entire process. Current forecasting techniques of energy consumption base their inferences on feeding ore mineralogical features, SAG dimensions, and operational variables.
More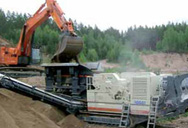
Investigation of the effect of filling level on the wear and
2022.4.1 Semi-autogenous grinding (SAG) mill is widely used in the grinding process of coal and ores because of its strong applicability, large capacity and low consumption of grinding media. ... Only 1–5% of the electrical energy consumed during the operation of the ball mill is used for the crushing of minerals (Cleary, 1998, Cleary, 2001c), and ...
More
Effect of particle shape and roughness of talc mineral
2004.2.16 Rod milling tests were conducted at 200×280 mm laboratory mill. During rod milling, 22.600 kg of stainless steel rods of 29, 24 and 19 mm in size were used as grinding media. Feed sizes of the minerals were −4750+3350 μm with a weight of 759.6 g. For autogenous grinding, a 420×225 mm laboratory scale autogenous mill with rubber
More
Minerals Free Full-Text Research on Grinding
2022.10.26 The particle size composition of grinding products will significantly affect the technical and economic indexes of subsequent separation operations. The polymetallic complex ores from Tongkeng and Gaofeng are selected as the research object in this paper. Through the JK drop-weight test, the batch grinding test, and the population-balance
More
Copper ore grinding in a mobile vertical roller mill pilot plant
2015.3.10 A study conducted by Gerold et al. (2012) showed that VRM was able to grind copper and slag with the energy saving of 22.9% and 34.4% respectively compared to conventional grinding circuits. Wear rate is another criterion that is needed to be considered. In this context, Erkan et al. (2012) in their study compared the wear rates of rod-ball ...
More
Minerals Free Full-Text The Effects of Ball-Mill Grinding ...
2023.9.9 In recent years, because of the decreasing liberation sizes of the minerals, processes such as grinding need to be evaluated in more detail. As is well known, size reduction processes are very important both in mineral processing and in many industrial applications. However, to increase the efficiency of the processes after size reduction,
More
Cascading (a) and cataracting (b) regimes in a tumbling mill
It consumes most of the energy used in mineral processing plants with grinding using up to 50% of the provided energy. Tumbling mills are an old technology that is still commonly used for grinding.
More