application of iron sinter

Recent Advances and Research Status in Energy Conservation of Iron
2017.9.19 It focuses on the development and application of energy-saving technologies such as the composite agglomeration process, sintering with high
More
Iron ore sintering - ScienceDirect
2015.1.1 Application of iron ore sinter. Sintering is the most economic and widely used agglomeration process for preparing iron ore fines for blast furnace use. The
More
Research and Application of Optimization Method for Iron
In view of iron and steel sintering ingredients, a comprehensive optimization method for iron and steel sintering ingredients is proposed. With the lowest cost Research and
More
Characteristics and Sintering Mechanisms of Iron
2023.4.27 The formation of silico-ferrite of calcium and aluminum (SFCA) and SFCA-I iron ore sinter phases during heating and cooling of synthetic iron ore sinter mixts. in the range 298 K to 1623 K (25 °C to
More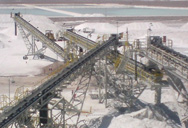
Minerals Special Issue : Mineralogy of Iron Ore
2019.5.20 Iron ore sintering is an important stage in the production of steel from iron ore. Sinter can constitute more than 60% of ferrous burden in modern blast furnaces in Japan and most blast furnaces in Europe.
More
Insight into the application of hydrogen-rich energy in iron
2020.3.1 Iron ore sintering process was the initial high temperature process, the task of which was to agglomerate fine iron ores into lump before smelting them into liquid iron
More
(PDF) Application of FactSage for iron sinter
2017.2.20 PDF The article demonstrates the opportunity to use thermodynamic modelling for understanding, prediction and optimisation of the iron sinter process.... Find, read and cite all the research ...
More
Application of steam injection in iron ore sintering: fuel
2023.1.9 Iron ore sin-tering is a crucial stage in the whole steelmaking flow, the function of which is to process iron ores (\ 8 mm) into lumpy sinter, thereby providing raw
More
Review of computational fluid dynamics modeling of iron
2022.9.1 Abstract. Iron ore sintering is a pretreatment step of smelting that agglomerates the iron ore using surface melting of green pellets to improve the quality of
More
Understanding iron ore analytical tools. – Process
2017.7.3 Iron Ore Analytical Tools in Application. Each of the seven tools listed in the above table can be used for improving mine performance and after Iron Ore 2017, ... (SFCA) and SFCA-I iron ore sinter bonding
More
Particle classification of iron ore sinter green bed mixtures
2023.2.1 The iron ore sintering process needs to be optimised to decrease its energy intensity and emissions of carbon and atmospheric pollutants, while continuing to produce sinter of sufficient quality for current and future low carbon blast furnace operations. Ideally, the sinter structure and mineralogy should be related back to the particle-level structure
More
Iron ore sintering - ScienceDirect
2022.1.1 Application of iron ore sinter. Sintering is the most economic and widely used agglomeration process for preparing iron ore fines for blast furnace use. The product of the sintering process is conveyed and charged into the blast furnace for production of hot metal. The counter-current principle on which the blast furnace operates makes it ...
More
Combustion behavior and influence mechanism of CO on iron
2014.6.14 The properties of circulating gas have a significant effect on sintering with flue gas recirculation, and the influence of CO in sintering process was investigated. The results show that the post-combustion of CO conducts in sinter zone when flue gas passes through the sintering bed, which releases much heat and reduces the consumption of
More
Prediction of sinter yield and strength in iron ore sintering
2018.2.25 Typically, a sinter pot test is used for measuring temperatures, which has a lower air leaking rate and a higher accuracy in contrast to sintering trolleys. A sinter pot test was conducted in this work with the operating parameters same as the simulation as listed in Table 3. The height of the sinter pot is 700 mm and the diameter is 300 mm.
More
Optimization of iron ore sintering process based on ELM
2017.8.1 In order to optimize the V-Ti blends for sinter TI,the basic sintering characteristics (BSCs) of 5 kinds of V-Ti ores , 2 ordinary ores and 3 groups of optimization V-Ti blends were studied .In ...
More
Quantitative XRD analysis and evaluation of iron ore, sinter,
2022.1.1 Abstract. Powder X-ray diffraction (XRD) is increasingly being used for the characterization of iron ore, sinter, and pellets thanks to the continuing developments in its instrumentation and software that enabled scientists and engineers to quickly analyze and quantify minerals and phases in often nonhomogeneous materials.
More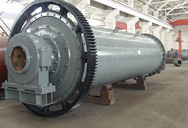
Investigation on the application of by-product steam in iron
2021.9.24 The results show that increasing the by-product steam injection concentration(0.32-0.47vol%) and prolonging the injection time(5min) within a proper range(10-15min) can improve sinter quality. 2 ...
More
Solids Free Full-Text SCORN: Sinter Composition
2022.7.12 Sinter composition optimization is an important process of iron and steel companies. To increase companies’ profits, they often rely on innovative technology or the workers’ operating experience to improve final productions. However, the former is costly because of patents, and the latter is error-prone. In addition, traditional linear
More
Processes Free Full-Text Experimental Production of Iron
2023.1.10 The application of waste tire char in metallurgical processes is an example of actions that form part of the circular economy and also of the appropriate use of anthropogenic resources that are technologically available. ... A. Biochars in iron ores sintering process: Effect on sinter quality and emission. Energies 2021, 14, 3749. [Google ...
More
Effect of Replacing Coke with Biomass Fuel on Sinter
2022.9.7 In the iron-ore-sintering process, the use of biomass charcoal instead of coke breeze can reduce the emission of flue gas pollutants and alleviate the energy crisis of fossil fuels. However, the direct application of biomass charcoal to iron ore sintering is bound to affect the sinter properties. The effects of biomass charcoal addition on the sintering
More
Recent Advances and Research Status in Energy Conservation of Iron
2017.9.19 For the ferrous burden of blast furnaces in China, sinter generally accounts for more than 70% and the sintering process accounts for approximately 6–10% of the total energy consumption of the iron and steel enterprise. Therefore, saving energy during the sintering process is important to reduce the energy consumption in the iron and steel
More
Modeling and simulation of mechanical degradation of iron ore sinter
2023.3.1 A sample of iron ore sinter was collected from a belt cut of the conveyor that feeds the industrial chute system of a plant located in India. Sinter particles are more prone to degradation than other iron agglomerates. ... Application of DEM to blending and homogeneity evaluation and improvement in a belt conveyor transfer chute system. 9th ...
More
Characteristics Evaluation and High Effective Utilization of
2021.8.27 The sinter Al 2 O 3 and total Fe contents were floated. The carefully weighed blend components of iron ores, sinter return, fluxes, and coke breeze were first dry mixed manually and then granulated for 4 min with addition of an appropriate amount of water (7.5–7.7%) for efficient granule formation in an electrically powered drum.
More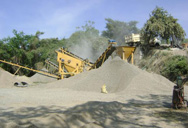
Automated optical image analysis of natural and sintered iron
2015.1.1 Another application of OIA is to characterize iron ore sinter. To study the behavior of ore fines during sintering or to study the reaction of certain fine ore blends with certain textural types of nucleus particles, compacted cylindrical tablets may be prepared (Ware et al., 2013, Clout and Manuel, 2003, Dehghan-Manshadi et al., 2014). These ...
More
A comprehensive characterization on the structural and
2015.11.5 Introduction. Sintered iron ores are consumed by most of the modern blast furnaces as the iron feed to the burdens [1]. Waste heat recovery from sintered ore particles (SOPs) is deemed to be a promising approach to improving the thermal efficiency and lowering the cost in iron and steel industry, which is realized practically using sinter
More
Application of machine learning algorithms for prediction of sinter ...
2021.12.15 The percentages of SiO 2, total Fe and CaO in iron ore fines, MgO in sinter and coke crushing index have a high positive impact on sinter machine productivity. When the percentage of total iron in iron ore fines increases from minimum of 59.62% to maximum 61.62%, the sinter plant productivity increases by 0.19 T/(m 2-h).
More
Insight into mechanisms of CaCl2 for improving
2022.11.15 The metallurgical performance of iron ore sinter, the primary feedstock for blast furnace (BF), particularly the reduction disintegration index (RDI) of sinter, has a significant impact on the BF ironmaking. ... (DFT) is a common tool that has a wide range of applications in material design, such as battery materials [21], [22], [23], alloy ...
More
Investigation into the characteristics of H - ScienceDirect
2019.7.5 Comprehensive evaluation of hydrogen-rich energy application in iron ore sintering process: Deep function mechanism analysis and process optimization. 2023, Journal of Cleaner Production. ... Iron ore sinter production is an important source of carbon emissions in China. Indeed, the uneven heat distribution in a sintering bed is a long
More
An intelligent integrated optimization system for the
2014.1.1 Different kinds of iron ore have different grades of iron, S contents, and prices. The iron ore mix, coke, limestone, dolomite, and returned sinter that is combined in the second proportioning phase have different contents of Fe, SiO 2, CaO, MgO, Al 2 O 3, S, and P that directly affect the chemical components of the raw mix, as well as the
More
Insight into the high proportion application of biomass fuel in iron ...
2019.9.20 Mixed iron ores main consisted of iron oxides, which was the main components of sinter, with its proportion closed to 65%. Dolomite, limestone, and quicklime were all Ca or Mg-bearing fluxes, with its purpose to produce sinter with desirable MgO content and basicity (mass ratio of CaO/SiO 2 ), which was an important factor for slag
More
Intensive carbon combustion in sintering packed bed via ...
2023.4.5 Improving the combustion efficiency of solid fuels is important for reducing carbon monoxide emissions in the iron ore sintering process. In this paper, the surface steam spraying technology is introduced in the sintering process based on the auxiliary combustion effect of steam on coke, and its potential to reduce carbon monoxide
More
Application of biomass fuel in iron ore sintering: influencing ...
The proportion of biomass fuel replacing coke breeze should, therefore, not exceed 40%, otherwise, the mineralisation of sinter material is insufficient and the yield and tumbler index of sinter significantly deteriorate. By increasing the size of biomass fuel, sinter indices are improved since the burning velocity of biomass fuel is optimised.
More
Sintering: A Step Between Mining Iron Ore and Steelmaking
2019.6.11 Sinter quality begins with the mined iron ore and the proper selection and mixing of the raw materials. Inhomogeneous raw mix can affect permeability and cause an increase in fuel consumption. During the iron ore sintering process in iron and steel manufacturing, an online analyzer can be used to determine the elemental composition
More
Application of steam injection in iron ore sintering: fuel
2023.1.9 iron and steel industry is still the pillar industry, vital to socioeconomic and sustainable development. Iron ore sin-tering is a crucial stage in the whole steelmaking flow, the function of which is to process iron ores (\8 mm) into lumpy sinter, thereby providing raw materials for iron-making [1–5]. The sintering heat originates from fuel
More
Metals Free Full-Text Research on Sinter Quality Prediction
2023.2.17 Sinter ore quality directly affects the stability of blast furnace production. In terms of both physical and chemical properties, the main indicators of sinter quality are the TFe content, alkalinity, and drum index. By analyzing the massive historical data on the sinter production of a steel company, this study proposes a sinter quality prediction
More
Optimization of iron ore sintering process based on ELM
2016.1.21 Optimization of iron ore sintering process is to maximize the productivity and the sinter ore quality while minimizing the energy consumption. However, these economic and technical criteria are sometimes contradictory and the improvement of one criterion generally leads to the deterioration of other criteria. This paper aims to seek the
More
Insight into the application of hydrogen-rich energy in iron
2020.3.1 During the process, water was added with 80 % of the total amount for stage-1, and the rest for stage-2. Before charging the granules into the sinter pot, 1 kg sinter of 10−16 mm was charged to form a hearth layer to protect the grate from thermal erosion. After that, an igniter was used to ignite the coke breeze in the surface layer, and the ...
More
Investigation on the application of by-product steam in iron
2022.4.12 The combustion-supporting effect of steam to coke breeze in sintering has the potential to improve sinter quality and reduce pollutants emissions. The results show that increasing the by-product steam injection concentration (0.32–0.47vol%) and prolonging the injection time (5 min) within a proper range (10–15 min) can improve sinter quality.
More
Comprehensive evaluation of sintering basic
2019.7.30 China Iron and Steel Research Institute Group 2019 Abstract Sintering basic characteristics of fourteen iron ores were comprehensively evaluated using micro-sinter and grey relational analysis methods. The results show that magnetite has a low assimilability, high bonding phase strength, and high crystal strength.
More