dry process of cement
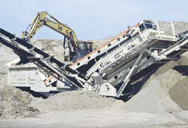
Manufacturing of Cement By Dry and Wet Process - Expert
The cement is manufactured by the following procedure:- Mixing of Raw Materials: In the wet process, there are two raw materials e. calcareous and argillaceous. Initially, Calcareous
More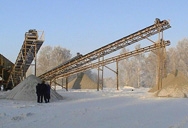
Cement Production - an overview ScienceDirect Topics
The production of cement is either through the wet or dry process with the dry process as the preferred option because of the lower energy intensity. Cement production accounts
More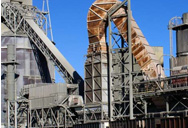
Dry process cement Britannica
In cement: Manufacture of cement are known as the wet, dry, and semidry processes and are so termed when the raw materials are ground wet and fed to the kiln as a slurry,
More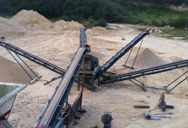
(PDF) Cement Manufacturing - ResearchGate
2015.12.9 Cement process include wet, dry, wet dry process and finish process. Roasting cement Considered one of the most important
More
Cement - Extraction, Processing, Manufacturing Britannica
The three processes of manufacture are known as the wet, dry, and semidry processes and are so termed when the raw materials are ground wet and fed to the kiln as a slurry,
More
Modernizing cement manufacturing in China leads to
2022.11.17 The cement manufacturing process mainly includes four steps: resource extraction, raw material preparation, clinker calcination, cement grinding 17,18, and fossil
More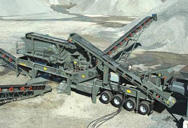
A comprehensive review on dry concrete: Application, raw
2022.9.1 Dry concrete, which can be understood literally, is defined as the fresh mixture of concrete having no flowability with a very small slump value. It is a hardened
More
Cement Manufacture - an overview ScienceDirect Topics
In the dry process, the moisture content of the raw material is reduced to less than 1% before the blending process occurs. The dry material is pulverized and fed to the rotary
More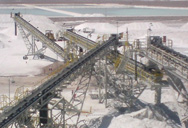
Cement Manufacturing—Technology, Practice, and
2021.11.17 There are four main types of processes used in cement manufacture: Dry Process, Semi-dry Process, Semi-wet Process, and the Wet process. In all these
More
2 Process Of Manufacture Of Cement - Wet
Wet process. Dry Process of Manufacture of Cement: Crushing of limestone and clay in crushers and stored in silos. Grinding of crushed materials and storing in hoppers. Mixing of materials by compressed air in the right
More
2 Types of Manufacturing of Cement - Wet and
2023.4.7 The dry process cement has a moisture level of 1% to 2%, which reduces the need for heat consumption during moisture evaporation It releases fewer greenhouse gases and other pollutants . This is because
More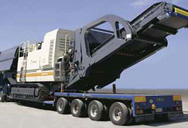
Review on energy conservation and emission reduction
2022.12.1 The dry process of cement manufacturing uses a raw meal containing up to 20% moisture by mass. However, the wet process uses slurry prepared by adding water to the raw meal. Nowadays, most cement industries prefer the dry method over the wet one because drying the moisture from the raw . Energy conservation approaches in cement
More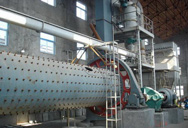
Cement grinding optimisation - ScienceDirect
2004.11.1 making cement by the chemical reaction between the components of the ground mixture. This chemical reaction occurs at high temperature in a rotary kiln, grinding the cement clinker nodules to 100% passing 90 μm in a dry circuit. Grinding occurs at the beginning and the end of the cement making process.
More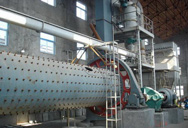
Dry Process of Cement Manufacturing Semi-dry Process
2022.4.8 Semi-dry Process of Cement Manufacturing. The blended meal will be sieved and then fed into the rotating dish in a semi-dry process. It is known to us as the granulator. The water content in this will also be about 12% of the meal being added simultaneously. As a result, the hard pellet, which is supposed to be about 15 mm in
More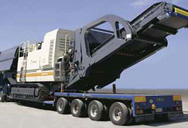
DETAILED DRY PROCESS OF CEMENT MANUFACTURING
4 天之前 Nowadays, we call the production line the new dry process cement production line with preheater and precalciner, which is the direction of growth of dry process cement production in future. Disadvantages: Disadvantages of the drying process are inconsistent mixing of raw materials, high power consumption and high dust content in the workshop.
More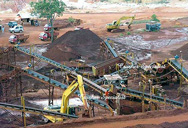
A Review on Pyroprocessing Techniques for Selected Wastes
2020.2.9 With this reason, many old wet process kilns have been converted into dry process plants. Mostly, semiwet and semidry process kilns are intermediate steps in the conversion. Over the years, wet process plants have been converted to dry ones especially in Europe. By 2004, dry process kilns accounted for 90% of all process technologies used.
More
(PDF) THE CEMENT MANUFACTURING PROCESS
They are mixed either dry (dry mixing) or by water (wet mixing). 3) Prepared raw mix is fed into the rotary kiln. 4) As the materials pass through the kiln their temperature is rised upto 1300-1600 °C. The process of heating is named as “burning”. The output is known as “clinker” which is 0.15-5 cm in diameter.
More
Process of Cement Manufacturing -A Brief into Dry and Wet Process
2023.6.14 The dry process is the most commonly used Cement manufacturing process today due to its energy efficiency. Here is a step-by-step procedure for the dry process of Cement manufacture: Quarrying and Crushing: The raw materials, such as Limestone, clay, shale, iron ore, and sometimes sand or bauxite, are extracted from
More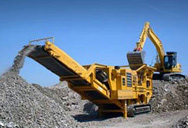
11.6 Portland Cement Manufacturing - US EPA
1971.8.17 Classification Code (SCC) for portland cement plants with wet process kilns is 3-05-006, and the six-digit SCC for plants with dry process kilns is 3-05-007. Portland cement accounts for 95 percent of the hydraulic cement production in the United States. The balance of domestic cement production is primarily masonry cement. Both of these
More
Cement Production Process Cement Manufacturing Process AGICO CEMENT
2020.8.25 The semi-dry process of cement also belongs to the dry process of cement, add certain water into raw meal powder to make raw meal ball, which will be sent into the vertical kiln to process cement clinker. The main advantage of dry process cement production is low heat consumption, it’s advantages include nonuniformity of raw meal,
More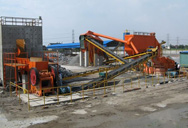
Cement Manufacturing—Technology, Practice, and
2021.11.17 The manufacturing of cement clinker was initially based on the “wet” process, but the “dry” process is today the state of the art. The “semi-wet” and “semi-dry” processes were intermediate. 4.1 The Dry Process. The raw meal is prepared by drying and grinding in ball mills or vertical roller mills.
More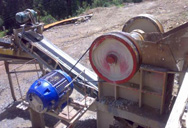
Manufacturing of cement PPT - SlideShare
2018.1.10 Manufacturing Processes Of Portland Cement There are 2-Types of Processes that can be used to Manufacture Portland Cement. Which are : Wet Process Dry Process 11. DRY Process • The both
More
Control of Precalciner Temperature in the Cement Industry:
2023.1.9 As the most critical equipment in the pre-calcination process of dry cement production, the temperature of the precalciner is an essential factor affecting the quality of cement. However, the cement calcination system is time-delayed, nonlinear, and multi-disturbance, which makes it difficult to predict and control the precalciner temperature. In
More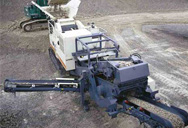
Dry Process Of Cement Production 300-5000TPD AGICO CEMENT
The dry process cement manufacturing process is widely utilized in the cement industry, it is a new method of manufacturing method in which fuel and power consumption has been reduced to a larger extent. Step 1: Raw material preparation.
More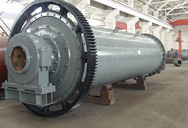
All Pakistan Cement Manufecturars Association
2023.7.27 The primary raw material for cement manufacture is calcium carbonate or limestone. This is obtained from the quarry where, after the removal of overburden, the rock is blasted, loaded into trucks and transported to the crusher. A multistage crushing process reduces the rock to stone less than 25 mm in diameter.
More
Portland Cement: Manufacturing, Properties, Types More
2024.1.3 Fig 1: Cement Manufacturing. The process of manufacturing cement involves mixing the calcareous and argillaceous components in a 3:1 ratio. Following by mixing of the materials, two processes can be followed to arrive at the final product of ordinary portland cement. ... Dry Process. It is a newly evolved process that is mostly
More
Manufacture Of Portland Cement Process Flow chart - civil
2019.11.30 Mixing of raw materials: The processes used for the manufacture of portland cement can be classified as dry and wet. In dry process. The raw materials are first reduced in size of about 25mm in crushers and Crushed material is ground to get fine particles into ball mill or tube mill. Each material after screening is stored in a separate
More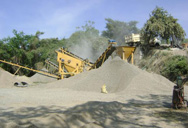
Cement manufacturing process PPT - SlideShare
2014.6.10 Evolution of the cement Process • Wet process easiest to control chemistry better for moist raw materials. • Wet process high fuel requirements - fuel needed to evaporate 30+% slurry water. • Dry process kilns less fuel requirements • Preheater/Precalciner further enhance fuel efficiency allow for high production rates.
More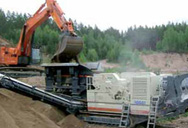
Comparison of Wet Process and Dry Process of Cement
In this paper we are discussing wet and dry process of Portland cement manufacture. Wet process minerals are wet ground to form a slurry and in dry process minerals are dry ground to form a powder like substance. In this paper, we are discussing the comparison between wet process and dry process with various advantages and disadvantages.
More
What is the manufacturing process of Portland
William Aspdin made what could be called ‘meso-Portland cement‘ (a mix of Portland cement and hydraulic lime).Isaac Charles Johnson further refined the production of ‘meso-Portland cement’ (middle stage of development),
More
ESSD - Global CO2 uptake by cement from 1930
2021.4.30 Pan et al. (2020) recently studied the emission reduction potential from producing cement mortar and concrete blocks by mixing in a high level of alkaline blending (e.g. blast furnace slag, fly ash, and mine
More
Why Choose Dry Process From Manufacturing
Dry process cement production kiln is the typical kiln type during the end of the 18th century and the beginning of the 19th century. It is a big step for haft kiln. Because of its less than 1% water content dust raw materials, it
More
Cement Manufacturing Process Phases Flow Chart Cement
2012.8.30 Cement Manufacturing Process Phase 1: Raw Material Extraction. Cement uses raw materials that cover calcium, silicon, iron and aluminum. Such raw materials are limestone, clay and sand. Limestone is for calcium. It is combined with much smaller proportions of sand and clay. Sand clay fulfill the need of silicon, iron and aluminum.
More
Fig. 12. Stages in cement production flow chart [43].
Stage 2: Crusher (grinding) The quarried material is reduced in size by compression and impacted in various mechanical crushers. Crushed rock is reduced in size from 120 cm to between 1.2 and 8 cm ...
More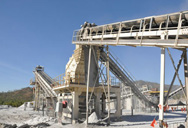
Electrified calciner concept for CO2 capture in pyro
2023.4.1 1. Introduction. The global cement industry has the second-largest share of the direct industrial CO 2 emission, emitting around 2.6 Gt of CO 2 in 2020 [1].Further, cement production is expected to grow by 12–23% by 2050 due to the rising world population and urbanization [2].The European Union (EU) aims to reduce greenhouse
More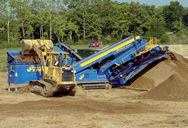
Comparison of Wet Process and Dry Process of Cement
2020.4.30 In this paper we are discussing wet and dry process of Portland cement manufacture. Wet process minerals are wet ground to form a slurry and in dry process minerals are dry ground to form a powder like substance. In this paper, we are discussing the comparison between wet process and dry process with various advantages and
More
5 Difference Between The Wet And Dry Process of
2019.5.24 Wet Process. 1. This method is adopted when the raw materials are soft. 2. The quality of cement prepared by this method is superior. 3. Wet process is the fasted method. 4. Raw materials are fed into the rotary kiln in the form of fine powder.
More
Wet Process vs. Dry Process Cement LUTON GROUP
5 天之前 Dry process cement is actually a dry-mixed mixture in which dry materials are uniformly mixed. Usually dry process cement is supplied in bulk or in bags. When used, it needs to be mixed with an appropriate amount of water or additives at the construction site. Dry process cement can be stored for a long time, usually 3-6 months. Production ...
More
Cement Production: How Cement Is Manufactured CEMEX UK
2. Transporting the raw material. Once the huge rocks have been fragmented, they are transported to the plant in dump trucks or by conveyor belt. 3. Crushing. The quarry stone is delivered through chutes to the crushers, where it is reduced by crushing or pounding to chunks approximately 1 ½ inches in size. 4.
More